Anti-abrasion composite cable material with enhanced tensile strength and preparing method thereof
A composite cable material and tensile strength technology, used in circuits, electrical components, plastic/resin/wax insulators, etc., can solve problems such as wear resistance, bending resistance, aging resistance, etc. Comprehensive performance, changing decomposition mode, good effect of corrosion resistance
- Summary
- Abstract
- Description
- Claims
- Application Information
AI Technical Summary
Problems solved by technology
Method used
Examples
Embodiment Construction
[0014] A wear-resistant composite cable material with enhanced tensile strength, made of the following raw materials in parts by weight (kg): high-density polyethylene 89, decabromodiphenyl ether 15, antimony trioxide 7, metallocene polyethylene 2, Nano-magnesium hydroxide 2, cyclohexane 4, γ-aminopropyltriethoxysilane 0.2, mica powder 5, POE elastomer 10, white wax oil 3, epoxy octyl stearate 2, glass beads 2, calcium sulfate Whisker 7, titanate coupling agent TMCTTS1, silane coupling agent kh4501.2, appropriate amount of water.
[0015] The wear-resistant composite cable material with enhanced tensile strength is made by the following specific steps:
[0016] (1) Add decabromodiphenyl ether and antimony trioxide into the high-speed mixer, mix at 80°C for 15 minutes, then add half of the amount of high-density polyethylene into the high-speed mixer, and mix at 90°C for 10 minutes Finally, put the mixed material in an open mill, masticate it at 145°C for 8 minutes to produce ...
PUM
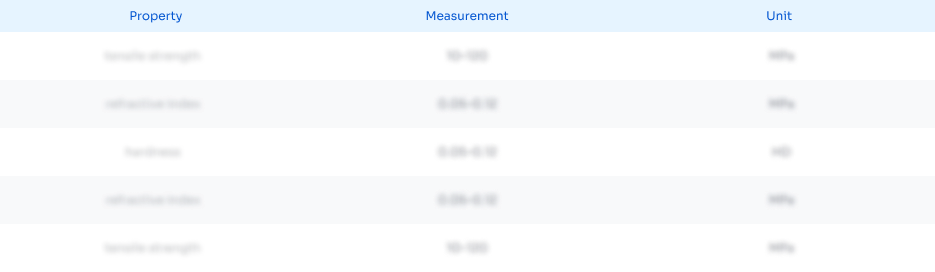
Abstract
Description
Claims
Application Information

- R&D
- Intellectual Property
- Life Sciences
- Materials
- Tech Scout
- Unparalleled Data Quality
- Higher Quality Content
- 60% Fewer Hallucinations
Browse by: Latest US Patents, China's latest patents, Technical Efficacy Thesaurus, Application Domain, Technology Topic, Popular Technical Reports.
© 2025 PatSnap. All rights reserved.Legal|Privacy policy|Modern Slavery Act Transparency Statement|Sitemap|About US| Contact US: help@patsnap.com