Method for preparing tetraphenylporphyrin through micro reaction device
A technology of tetraphenylporphyrin and micro-reaction device, which is applied in the direction of organic chemistry, can solve the problems of high reaction temperature, substrate limitation, harsh reaction conditions for synthesizing porphyrin, complex post-treatment, etc., and achieve high-efficiency heat and mass transfer capabilities , easy to directly enlarge, the effect of small reaction volume
- Summary
- Abstract
- Description
- Claims
- Application Information
AI Technical Summary
Problems solved by technology
Method used
Image
Examples
Embodiment 1
[0028] In the microchannel reaction device, the inner diameter of the pipeline in the reactor and the inner diameter of the connecting pipe are both 1mm, the length of the connecting pipe between the feed liquid inlet and the microchannel reactor is 32cm, and the connecting pipe between the microreactor and the feed liquid outlet The length is 30cm; the volume of the microchannel reactor is 10mL; the type of the mixing valve is Y-type.
[0029] Take 0.8mmol of benzaldehyde, 0.8mmol of pyrrole, and 8mmol of absolute ethanol, and add it to 50mL of dichloromethane to make a uniform solution; take 0.32mmol of boron trifluoride ether, add it to 50mL of dichloromethane to make a solution. The two materials are mixed and pumped into the microchannel reactor through the mixing valve. The flow rate of the two pumps is controlled to be 0.167mL / min, and the two streams of materials flow through the microreactor at the same time. In the flask of base benzoquinone, collect 50ml and change...
Embodiment 2
[0031] In the microchannel reaction device, the inner diameter of the pipeline in the reactor and the inner diameter of the connecting pipe are both 0.8mm, the length of the connecting pipe between the feed liquid inlet and the microchannel reactor is 10cm, and the connection between the microreactor and the feed liquid outlet The tube length is 33 cm; the volume of the microchannel reactor is 5 mL; the type of mixing valve is Y type.
[0032] Take 0.8mmol of benzaldehyde, 0.8mmol of pyrrole, and 8mmol of absolute ethanol, and add it to 50mL of dichloromethane to make a uniform solution; take 0.28mmol of boron trifluoride ether, add it to 50mL of dichloromethane to make a solution. The two materials are mixed and pumped into the microchannel reactor through the mixing valve. The flow rate of the two pumps is controlled to be 0.167mL / min, and the two materials flow through the microreactor at the same time. The temperature of the reactor is 30°C, and the reaction residence time...
Embodiment 3
[0034] In the microchannel reaction device, the inner diameter of the pipeline in the reactor and the inner diameter of the connecting pipe are both 1.2mm, the length of the connecting pipe between the feed liquid inlet and the microchannel reactor is 38cm, and the connection between the microreactor and the feed liquid outlet The length of the tube is 25 cm; the volume of the microchannel reactor is 10 mL; the type of the mixing valve is inverted Y.
[0035] Take 1.2mmol of benzaldehyde, 1.2mmol of pyrrole, and 10mmol of absolute ethanol, and add it to 50mL of dichloromethane to make a uniform solution; take 0.32mmol of boron trifluoride ether, and add it to 50mL of dichloromethane to make a solution. The two materials are mixed and pumped into the microchannel reactor through the mixing valve. The flow rate of the two pumps is controlled to be 0.2mL / min, and the two materials flow through the microreactor at the same time. The temperature of the reactor is 30°C, and the reac...
PUM
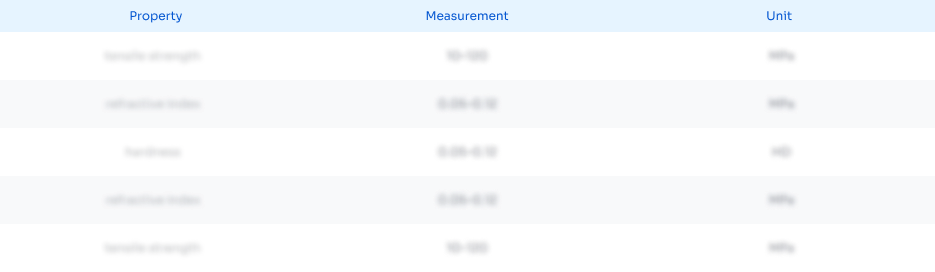
Abstract
Description
Claims
Application Information

- R&D
- Intellectual Property
- Life Sciences
- Materials
- Tech Scout
- Unparalleled Data Quality
- Higher Quality Content
- 60% Fewer Hallucinations
Browse by: Latest US Patents, China's latest patents, Technical Efficacy Thesaurus, Application Domain, Technology Topic, Popular Technical Reports.
© 2025 PatSnap. All rights reserved.Legal|Privacy policy|Modern Slavery Act Transparency Statement|Sitemap|About US| Contact US: help@patsnap.com