Preparing method for ultra-fine hard alloy
A cemented carbide and inhibitor technology, applied in the field of powder metallurgy, can solve the problems of high production cost and complicated process, and achieve the effects of long service life, simple process and low cost
- Summary
- Abstract
- Description
- Claims
- Application Information
AI Technical Summary
Problems solved by technology
Method used
Image
Examples
Embodiment 1
[0030] A high-performance ultra-fine cemented carbide A for processing cast iron, common steel and titanium alloys, the weight percentage of the alloy is: 10% of Co powder with Fsss particle size of 1.41 μm, and WC with Fsss particle size (BET) of 0.35 μm Powder 89.5%, Cr with Fsss particle size 1.5μm 3 C 2 Inhibitor 0.5%.
[0031] After cleaning the ball mill and the hard alloy baseball, add Cr 3 C 2 Inhibitor, all Co powder and some alcohol, the amount of alcohol added is 120ml / 100g Co powder, pre-dispersed for 2h. After the pre-dispersion, WC powder with Fsss particle size (BET) of 0.35 μm was added, and the corresponding alcohol was added. The final liquid-solid ratio was 320ml / Kg, the ball-material ratio was 4.3:1, and the ball milling time was 35h. After wet grinding, it is spray-dried and pressed into shape. The pressed green compact was sintered at 1440°C under a pressure of 50 bar and held for 1 hour to obtain the final alloy. The metallographic structure of the...
Embodiment 2
[0033] A high-performance ultra-fine hard alloy B is used for processing cast iron and stainless steel. The weight percentage of the alloy is: 10.5% of Co powder with Fsss particle size of 1.41 μm, 88.85% of WC powder with Fsss particle size (BET) of 0.35 μm, Cr with an Fsss particle size of 1.5 μm 3 C 2 Inhibitor 0.65%.
[0034] After cleaning the ball mill cylinder and hard alloy baseball, add Cr 3 C 2 Inhibitor, all Co powder and some alcohol, the amount of alcohol added is 140ml / 100g Co powder, pre-dispersed for 2h. After the pre-dispersion, WC powder with Fsss particle size (BET) of 0.35 μm was added, and the corresponding alcohol was added. The final liquid-solid ratio was 350ml / Kg, the ball-to-material ratio was 4.5:1, and the ball milling time was 40h. After wet grinding, it is spray-dried and pressed into shape. The pressed green compact was sintered at 1440°C under a pressure of 50 bar and held for 1 hour to obtain the final alloy. The metallographic structure ...
Embodiment 3
[0036] A high-performance ultra-fine cemented carbide C is used for processing cast iron and stainless steel. The weight percentage of the alloy is: 10% of Co powder with Fsss particle size of 1.41 μm, 89.2% of WC powder with Fsss particle size (BET) of 0.25 μm, Cr with an Fsss particle size of 1.5 μm 3 C 2 Inhibitor 0.3%, TaC inhibitor with Fsss particle size 1.5 μm 0.5%.
[0037] After cleaning the ball mill cylinder and hard alloy baseball, add Cr 3 C 2And TaC inhibitor, all Co powder and some alcohol, the amount of alcohol added is 150ml / 100g Co powder, pre-dispersed for 3h. After the pre-dispersion, WC powder with Fsss particle size (BET) of 0.25 μm was added, and the corresponding alcohol was added. The final liquid-solid ratio was 375ml / Kg, the ball-material ratio was 4.8:1, and the ball milling time was 45h. After wet grinding, it is spray-dried and pressed into shape. The pressed compact was sintered at 1460° C. under a pressure of 50 bar and held for 1 hour to o...
PUM
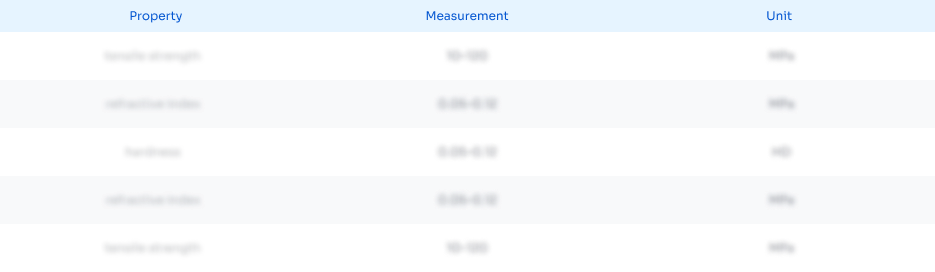
Abstract
Description
Claims
Application Information

- Generate Ideas
- Intellectual Property
- Life Sciences
- Materials
- Tech Scout
- Unparalleled Data Quality
- Higher Quality Content
- 60% Fewer Hallucinations
Browse by: Latest US Patents, China's latest patents, Technical Efficacy Thesaurus, Application Domain, Technology Topic, Popular Technical Reports.
© 2025 PatSnap. All rights reserved.Legal|Privacy policy|Modern Slavery Act Transparency Statement|Sitemap|About US| Contact US: help@patsnap.com