Tin tetrachloride production device with wave tube reactor
A technology of tin tetrachloride and production device, applied in directions such as tin chloride, tin halide, etc., can solve problems such as heat release, influence reaction speed, difficulty, etc., and achieve increased reaction contact area, improved reaction speed, environmental The effect of pollution reduction
- Summary
- Abstract
- Description
- Claims
- Application Information
AI Technical Summary
Problems solved by technology
Method used
Image
Examples
Embodiment Construction
[0023] In order to make the content of the present invention more obvious and easy to understand, the present invention will be described in detail below with reference to specific embodiments.
[0024] As shown in the figure, the tin tetrachloride production device with a wave tube reactor includes a tin melting furnace 1, a pressurized tank 2, a condensation pipe 3, a chlorine storage tank, a cyclone tank 4 and a product storage tank 5. The top of the tin furnace 1 is provided with a feeding port 6, the bottom of the tin melting furnace 1 is connected with the pressurized tank 2 through a tin liquid feeder 7, and a wave tube reactor is provided inside the tin melting furnace 1, and the wave tube reactor includes a pipe body. The reaction pipe 8 is a wave-shaped pipe body, two inlet pipes 9 arranged at one end of the reaction pipe 8, and a product outlet pipe 10 arranged at the other end of the reaction pipe 8; the bottom of the pressurized tank 2 is connected with a tin liqui...
PUM
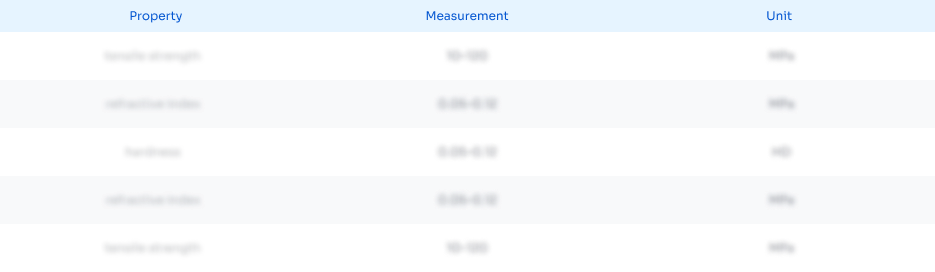
Abstract
Description
Claims
Application Information

- R&D
- Intellectual Property
- Life Sciences
- Materials
- Tech Scout
- Unparalleled Data Quality
- Higher Quality Content
- 60% Fewer Hallucinations
Browse by: Latest US Patents, China's latest patents, Technical Efficacy Thesaurus, Application Domain, Technology Topic, Popular Technical Reports.
© 2025 PatSnap. All rights reserved.Legal|Privacy policy|Modern Slavery Act Transparency Statement|Sitemap|About US| Contact US: help@patsnap.com