Carbon fiber composite material heating and curing process
A composite material and heat curing technology, which is applied in the field of carbon fiber composite material heat curing technology, can solve the problems of large residual stress of composite material components, component deformation, complex temperature field, etc., and achieve significant beneficial effects, high pass rate, and production cost control Effect
- Summary
- Abstract
- Description
- Claims
- Application Information
AI Technical Summary
Problems solved by technology
Method used
Examples
Embodiment 1
[0022] Carry out the heating and curing process of carbon fiber composite materials according to the following steps:
[0023] Step 1, vacuumize, put the carbon fiber composite material into the curing device, vacuumize to less than -0.8bar, and maintain for 2min;
[0024] Step 2: pressurize and heat up, raise the ambient temperature in the curing device to 122°C, the temperature rise rate is 1.0°C / min, and pressurize to 1.2bar at the same time, when the temperature of the thermocouple on the composite material reaches 122°C, maintain the ambient temperature at all times 5°C higher than the temperature of the thermocouple;
[0025] Step 3, when the temperature of the thermocouple on the composite material in step 2 rises to 140°C, keep warm and pressurize, and under the pressure conditions of step 2, continue to pressurize to 3.5bar, and keep the constant pressure for 120min;
[0026] Step 4, lower the temperature and pressure, slowly lower the ambient temperature according t...
Embodiment 2
[0028] Carry out the heating and curing process of carbon fiber composite materials according to the following steps:
[0029] Step 1, vacuumize, put the carbon fiber composite material into the curing device, vacuumize to less than -0.8bar, and maintain for 5min;
[0030] Step 2: pressurize and heat up, raise the ambient temperature in the curing device to 125°C, the temperature rise rate is 2.0°C / min, and pressurize to 1.2bar at the same time, when the temperature of the thermocouple on the composite material reaches 122°C, maintain the ambient temperature at all times 4°C higher than the thermocouple temperature;
[0031] Step 3, when the temperature of the thermocouple on the composite material in step 2 rises to 140°C, keep warm and pressurize, and under the pressure conditions of step 2, continue to pressurize to 3.8bar, and keep the constant pressure for 100min;
[0032] Step 4, lower the temperature and pressure, slowly lower the ambient temperature according to the t...
Embodiment 3
[0034] Carry out the heating and curing process of carbon fiber composite materials according to the following steps:
[0035] Step 1, vacuumize, put the carbon fiber composite material into the curing device, vacuumize to less than -0.8bar, and maintain the time for 10min;
[0036] Step 2: pressurize and heat up, raise the ambient temperature in the curing device to 127°C, the temperature rise rate is 2.0°C / min, and pressurize to 2.0bar at the same time, when the temperature of the thermocouple on the composite material reaches 125°C, maintain the ambient temperature at all times 2°C higher than the thermocouple temperature;
[0037] Step 3, when the temperature of the thermocouple on the composite material in step 2 rises to 140°C, keep warm and pressurize, and under the pressure conditions of step 2, continue to pressurize to 4.0 bar and keep the pressure constant for 130 minutes;
[0038] Step 4, lower the temperature and pressure, slowly lower the ambient temperature acc...
PUM
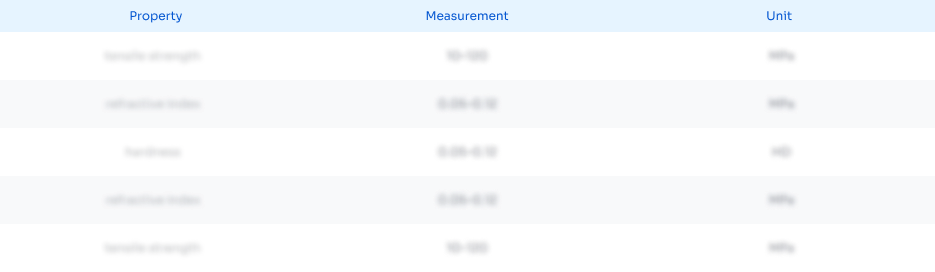
Abstract
Description
Claims
Application Information

- Generate Ideas
- Intellectual Property
- Life Sciences
- Materials
- Tech Scout
- Unparalleled Data Quality
- Higher Quality Content
- 60% Fewer Hallucinations
Browse by: Latest US Patents, China's latest patents, Technical Efficacy Thesaurus, Application Domain, Technology Topic, Popular Technical Reports.
© 2025 PatSnap. All rights reserved.Legal|Privacy policy|Modern Slavery Act Transparency Statement|Sitemap|About US| Contact US: help@patsnap.com