Graphene-modified epoxy zinc-rich primer and preparation method thereof
A technology of epoxy zinc-rich primer and graphene modification, applied in epoxy resin coatings, coatings, anti-corrosion coatings, etc., to achieve the effect of dense paint film and enhanced anti-corrosion effect
- Summary
- Abstract
- Description
- Claims
- Application Information
AI Technical Summary
Problems solved by technology
Method used
Image
Examples
Embodiment 1
[0024] 1. Preparation of modified epoxy resin Phthalic acid modified epoxy resin:
[0025] Put 100Kg of epoxy resin into the reactor, stir and heat to 80°C, add 5Kg of phthalic anhydride, continue to stir, keep warm at 80°C for 15 minutes, and cool down to obtain phthalic acid epoxy resin.
[0026] Two, prepare graphene epoxy resin slurry:
[0027] The phthalic acid epoxy resin 19Kg prepared by step (1) is dropped in the mixing tank, add graphene 0.5Kg and stir at a high speed for half an hour, become uniform paste, promptly make graphene epoxy resin slurry;
[0028] 3. Preparation of graphene-modified epoxy zinc-rich primer:
[0029] Slowly stir again, drop into solvent toluene 6Kg successively, butanol 4Kg, anti-sedimentation agent organic bentonite 0.5Kg, zinc powder 85Kg, disperse at high speed for half an hour, adjust viscosity, filter and obtain epoxy zinc-rich primer.
[0030] When the paint is used, component A is epoxy zinc-rich primer, component B is 30% phenalkami...
Embodiment 2
[0032] 1. Preparation of modified epoxy resin Phthalic acid modified epoxy resin:
[0033] Put 100Kg of epoxy resin into the reactor, stir and heat to 80°C, add 8Kg of phthalic anhydride, continue to stir, keep warm at 80°C for 15 minutes and cool down to obtain phthalic acid epoxy resin.
[0034] Two, prepare graphene epoxy resin slurry:
[0035] The phthalic acid epoxy resin 25Kg prepared by step (1) is dropped into the mixing tank, add graphene 0.8Kg and stir at a high speed for half an hour, and become uniform paste, that is, graphene epoxy resin slurry is obtained;
[0036] 3. Preparation of graphene-modified epoxy zinc-rich primer:
[0037] Stir slowly again, drop into solvent toluene 8Kg successively, butanol 5Kg, anti-sedimentation agent polyamide wax 0.8Kg, zinc powder 88Kg, disperse at high speed for half an hour, adjust viscosity, filter and obtain epoxy zinc-rich primer.
[0038] When the paint is used, component A is epoxy zinc-rich primer, component B is 30% ph...
Embodiment 3
[0040] 1. Preparation of modified epoxy resin Phthalic acid modified epoxy resin:
[0041] Put 100Kg of epoxy resin into the reactor, stir and heat to 80°C, add 10Kg of phthalic anhydride, continue to stir, keep warm at 85°C for 15 minutes and cool down to obtain phthalic acid epoxy resin.
[0042] Two, prepare graphene epoxy resin slurry:
[0043] The phthalic acid epoxy resin 16Kg prepared by step (1) is dropped in the mixing tank, add graphene 1.1Kg and stir at a high speed for half an hour, become uniform paste, promptly make graphene epoxy resin slurry;
[0044] 3. Preparation of graphene-modified epoxy zinc-rich primer:
[0045] Stir slowly again, drop into solvent toluene 7Kg successively, butanol 3Kg, anti-sedimentation agent polyamide wax 0.6Kg, zinc powder 75Kg, disperse at high speed for half an hour, adjust viscosity, filter and obtain epoxy zinc-rich primer.
[0046] When the paint is used, component A is epoxy zinc-rich primer, component B is 30% phenalkamine (...
PUM
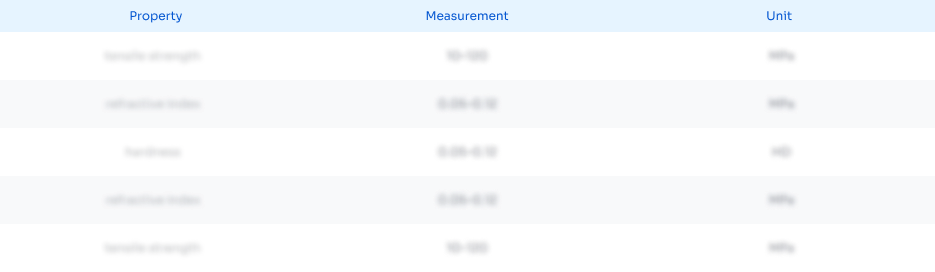
Abstract
Description
Claims
Application Information

- Generate Ideas
- Intellectual Property
- Life Sciences
- Materials
- Tech Scout
- Unparalleled Data Quality
- Higher Quality Content
- 60% Fewer Hallucinations
Browse by: Latest US Patents, China's latest patents, Technical Efficacy Thesaurus, Application Domain, Technology Topic, Popular Technical Reports.
© 2025 PatSnap. All rights reserved.Legal|Privacy policy|Modern Slavery Act Transparency Statement|Sitemap|About US| Contact US: help@patsnap.com