Preparation method for alumina carrier
A kind of technology of alumina carrier and carrier, which is applied in the direction of catalyst carrier, chemical instrument and method, chemical/physical process, etc., can solve the problems of catalyst deactivation, catalyst blockage, etc., and achieve the goal of increasing pore volume, good support, and preventing collapse Effect
- Summary
- Abstract
- Description
- Claims
- Application Information
AI Technical Summary
Problems solved by technology
Method used
Image
Examples
example 1
[0025] Weigh 100g of pseudo-boehmite dry rubber powder (produced by Wenzhou Jingjing Alumina Co., Ltd., with a water absorption rate of 1.2ml / g) and place it in a beaker, and add 200mL of 25% xylitol aqueous solution to the beaker for immersion. 4 hours. The impregnated material was filtered, and the filter cake was transferred to an autoclave and sealed at 140° C. for 10 hours. After drying, the processed material is kneaded uniformly with 5 g of succulent powder and an appropriate amount of 5% citric acid aqueous solution, and then extruded into strips. The shaped wet strips were dried at 120°C for 8 hours. The dried carrier is put into the spray rolling pot, and in the rotating state, 80 ml of the solution containing 1.6 grams of ammonium oxalate and 8 grams of phosphoric acid is sprayed and soaked to the carrier in the rolling pot by atomization. The mass concentration of ammonium ions in the solution is 0.6%, and the mass ratio of phosphoric acid to ammonium oxalate is ...
example 2
[0027] The same as Example 1, except that the mixed aqueous solution of sorbitol and mannitol with a mass concentration of 40% and a mass ratio of 1:1 was used for dipping for 3 hours. The temperature of the carbonization treatment was 130° C. for 14 hours of sealing treatment. When spraying phosphoric acid and ammonium oxalate solution, use 50ml of unsaturated spray dipping solution containing 1.5 g of ammonium oxalate and 10.5 g of phosphoric acid for the first spray impregnation (the mass concentration of ammonium ions in the solution is 0.9%, phosphoric acid and oxalic acid) The mass ratio of ammonium is 7:1), the temperature of the first sealing heat treatment is 120 ° C, the treatment time is 10 hours, and the second spray impregnation is 30ml of the above solution unsaturated spray impregnation. The temperature of the second sealing heat treatment is 150° C. and the treatment time is 6 hours, and the alumina carrier A2 of the present invention is prepared.
example 3
[0029] The same as Example 1, except that the mixed aqueous solution of glucose and ribose with a mass concentration of 30% and a mass ratio of 1:1 was used for dipping for 5 hours. The temperature of the carbonization treatment was 120° C. for 16 hours of sealing treatment. When spraying phosphoric acid and ammonium oxalate solution, the first unsaturated spray impregnation is unsaturated spray impregnation with 60ml of a solution containing 2.4 g of ammonium oxalate and 7.2 g of phosphoric acid (the mass concentration of ammonium ions in the solution is 1.2%, phosphoric acid The mass ratio to ammonium oxalate is 3:1), the temperature of the first sealing heat treatment is 160 ° C, the treatment time is 6 hours, and the second spray impregnation is impregnated with 20ml of the above solution unsaturated spray impregnation. The temperature of the second sealing heat treatment was 130° C. and the treatment time was 12 hours, and the alumina carrier A3 of the present invention w...
PUM
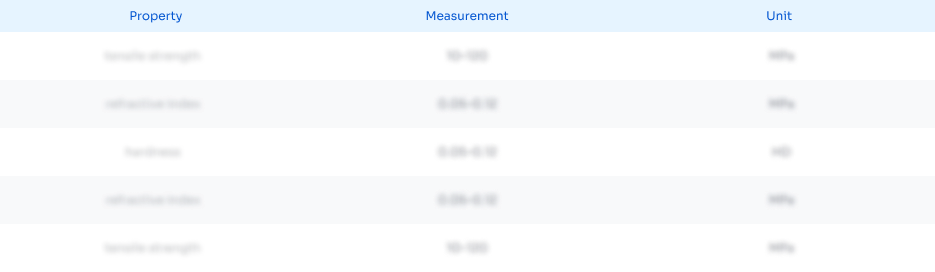
Abstract
Description
Claims
Application Information

- R&D Engineer
- R&D Manager
- IP Professional
- Industry Leading Data Capabilities
- Powerful AI technology
- Patent DNA Extraction
Browse by: Latest US Patents, China's latest patents, Technical Efficacy Thesaurus, Application Domain, Technology Topic, Popular Technical Reports.
© 2024 PatSnap. All rights reserved.Legal|Privacy policy|Modern Slavery Act Transparency Statement|Sitemap|About US| Contact US: help@patsnap.com