A method and system for flue gas denitrification and dust removal
A technology for denitrification, dust removal and flue gas, which is applied in the field of flue gas purification, can solve the problems of insufficient denitrification efficiency, easy thermal shock fragmentation, poor overall temperature resistance, etc., to ensure catalytic filtration effect, improve denitrification efficiency, and increase retention the effect of time
- Summary
- Abstract
- Description
- Claims
- Application Information
AI Technical Summary
Problems solved by technology
Method used
Image
Examples
Embodiment 1
[0046] Embodiment 1 discloses a method for denitration and dust removal of flue gas, including the steps:
[0047] S10: adding a reducing agent to the flue gas to obtain a first flue gas, where the first flue gas includes dust, nitrogen oxides and a reducing agent;
[0048] S20: Pass the first flue gas through the catalytic filter assembly, the dust in the first flue gas is intercepted on the surface of the catalytic filter assembly to form a filter cake, and the reducing agent and nitrogen oxides in the first flue gas are denitrified in the catalytic filter assembly The reaction generates nitrogen and water to obtain clean flue gas;
[0049] S30: Expel the clean flue gas.
[0050] The method for denitration and dust removal of flue gas of the present invention obtains the first flue gas by adding a reducing agent to the flue gas, and makes the first flue gas pass through the catalytic filter assembly, thereby removing nitrogen oxides and dust in the first flue gas. The flue...
Embodiment 2
[0052] Compared with the first embodiment, the improvement of the second embodiment is that the method for denitration and dust removal of the flue gas in the second embodiment further includes step S40: collecting the dust filter cake on the surface of the catalytic filter assembly.
[0053] By regularly collecting dust filter cake on the surface of the catalytic filter assembly, the catalytic filter assembly can be effectively cleaned, thereby ensuring the catalytic filtering effect of the catalytic filter assembly to a certain extent.
Embodiment 3
[0055] Compared with the first embodiment, the improvement of the third embodiment is that in the method for denitration and dust removal of the flue gas in the third embodiment, in step S10, the added reducing agent and the NO in the flue gas are added. X The molar ratio is 1:1~1.1:1. If the reducing agent and NO in the flue gas X If the ratio of the molar ratio is too small, the denitration reaction will not be completely complete, and if the ratio is too large, the ammonia escape will exceed the standard.
[0056] In step S20, when the reducing agent in the first flue gas undergoes a denitration reaction in the catalytic filter assembly, the reaction temperature is 250-380°C. If the reaction temperature of the denitration reaction is too high, the catalyst will be deactivated by sintering. If the reaction temperature is too low, the reaction rate will be too slow and the denitration efficiency will be low.
[0057] In this embodiment, the reducing agent is ammonia gas, li...
PUM
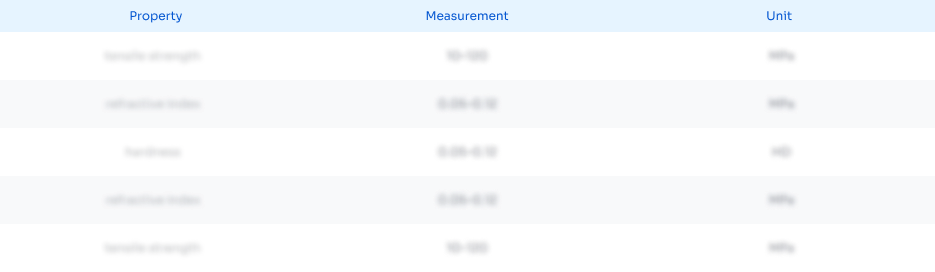
Abstract
Description
Claims
Application Information

- R&D Engineer
- R&D Manager
- IP Professional
- Industry Leading Data Capabilities
- Powerful AI technology
- Patent DNA Extraction
Browse by: Latest US Patents, China's latest patents, Technical Efficacy Thesaurus, Application Domain, Technology Topic, Popular Technical Reports.
© 2024 PatSnap. All rights reserved.Legal|Privacy policy|Modern Slavery Act Transparency Statement|Sitemap|About US| Contact US: help@patsnap.com