Electrochemical machining method, electrochemical machining device, and electrochemical machining solution
A processing method and technology for processing fluid, which are applied in the field of electrolytic machining of superhard alloys, and can solve the problems of deterioration of electrolytic machining fluid, inability to continue processing, and failure to establish a sediment treatment method.
- Summary
- Abstract
- Description
- Claims
- Application Information
AI Technical Summary
Problems solved by technology
Method used
Image
Examples
Embodiment approach 1
[0040]As mentioned above, the conventional electrolytic machining of cemented carbide has problems in that machining cannot be performed due to insufficient sodium ions during machining, and that tungsten, which is a valuable resource, cannot be recovered. In the present invention, the electrolytic machining method is to apply a voltage to the electrode as a negative electrode between the electrode and the workpiece, that is, the cemented carbide, so that a current flows, thereby anodizing the tungsten carbide (WC), which is the component of the workpiece, the cemented carbide (WC) Tungsten oxide (WO3) is formed, cobalt (Co) is electrolytically smelted, and tungsten oxide (WO3) produced by anodic oxidation is chemically dissolved for processing. In this electrolytic processing method, attention is paid to tungstic acid Ions (WO42-) react with calcium (Ca) ions. That is, sodium tungstate (Na2WO4), which is a product of electrolytic machining of cemented carbide, is water-solubl...
Embodiment approach 2
[0050] In Embodiment 1, the recovery of tungsten was described, but in Embodiment 2, it relates to an effective recovery method for other metal components and the like. In addition, it can have the same structure as other embodiment unless it specifically limits.
[0051] Co, Ti, Ta, etc. initially become chlorides in the reaction of electrolytic processing, forming CoCl2, TiC2, TaCl2, and as time goes by, form hydroxides, release Cl ions, and regenerate NaCl, so the electrolyte returns to the original electrolysis liquid. These metals can also be recovered in the state of hydroxides, but in this case, they are recovered as precipitates, which are bulky and the subsequent treatment is troublesome. In order to regenerate Co, Ti, and Ta as regenerated resources, it is preferable to recover them in a highly pure metal state, and attention is paid to electrodeposition. However, if the reaction is excessively performed in the hydroxide in order to perform electrodeposition effici...
Embodiment approach 3
[0070] In Embodiment 1, a method of recovering tungsten (W) in electrolytic machining of cemented carbide was described. This method is to use the electrode as the negative electrode, anodize tungsten carbide (WC) to become tungsten oxide (WO3), and at the same time electrolytically dissolve cobalt (Co), and oxidize the anode to produce tungsten oxide (WO3) chemically. The method of dissolving and processing is not necessarily limited to the case where the electrode is used as a positive electrode and the electrode is used as a negative electrode. The state is alternately repeated. However, in consideration of processing efficiency, it is preferable to use the electrode as a positive electrode to attract Na+ to the workpiece side and actively dissolve tungsten oxide (WO3). Embodiment 3 relates to a processing method while switching electrode polarity between positive and negative electrodes. In addition, it can have the same structure as other embodiment unless it specificall...
PUM
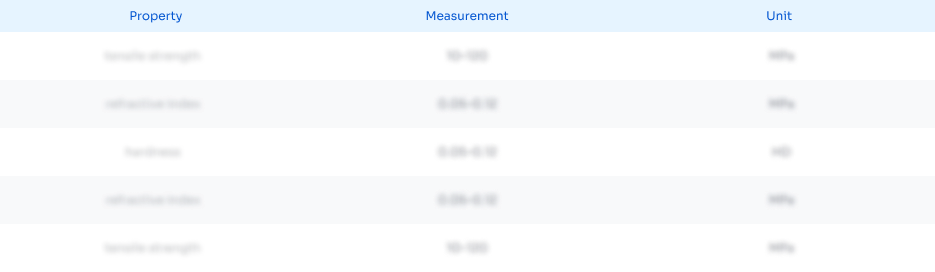
Abstract
Description
Claims
Application Information

- R&D
- Intellectual Property
- Life Sciences
- Materials
- Tech Scout
- Unparalleled Data Quality
- Higher Quality Content
- 60% Fewer Hallucinations
Browse by: Latest US Patents, China's latest patents, Technical Efficacy Thesaurus, Application Domain, Technology Topic, Popular Technical Reports.
© 2025 PatSnap. All rights reserved.Legal|Privacy policy|Modern Slavery Act Transparency Statement|Sitemap|About US| Contact US: help@patsnap.com