Pipe welding heat treatment process
A process and pipeline technology, applied in the field of pipeline welding heat treatment process, can solve the problems of large structural rigidity, large steel pipe diameter, burning loss of metal alloy elements, etc.
- Summary
- Abstract
- Description
- Claims
- Application Information
AI Technical Summary
Problems solved by technology
Method used
Examples
Embodiment Construction
[0021] Below in conjunction with embodiment the present invention will be further described, and its operating steps are as follows:
[0022] A pipe welding heat treatment process, the process includes the following process requirements:
[0023] (1) Argon arc welding, at an ambient temperature above 0°C, the preheating temperature is 100~150°C;
[0024] (2) During the welding process, the interlayer temperature is 200~300°C;
[0025] (3) After the overall welding of the weld seam is completed, heat treatment should be performed after the weldment is cooled to 100~120°C and kept at a constant temperature for 1~2 hours. When the welded joint cannot be heat treated in time, it should be heated immediately after welding. 250~350℃, heat treatment after constant temperature time, the constant temperature time should be calculated according to the wall thickness of the base metal: calculated as 1h / 25mm, but not less than 4 hours;
[0026] (4) The heating width of the heat treatmen...
PUM
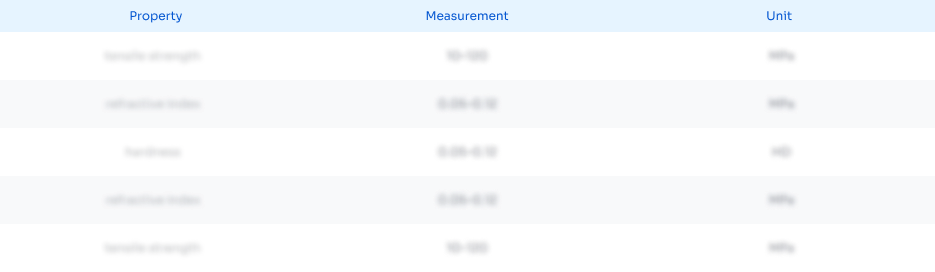
Abstract
Description
Claims
Application Information

- Generate Ideas
- Intellectual Property
- Life Sciences
- Materials
- Tech Scout
- Unparalleled Data Quality
- Higher Quality Content
- 60% Fewer Hallucinations
Browse by: Latest US Patents, China's latest patents, Technical Efficacy Thesaurus, Application Domain, Technology Topic, Popular Technical Reports.
© 2025 PatSnap. All rights reserved.Legal|Privacy policy|Modern Slavery Act Transparency Statement|Sitemap|About US| Contact US: help@patsnap.com