Glass fiber compound surface skin and production method
A composite surface, glass fiber technology, applied in the field of glass fiber composite surface skin and production, can solve the problems of single raw material density, insufficient hardness, etc., and achieve the effect of not easy to be old, high density, easy to process and form
- Summary
- Abstract
- Description
- Claims
- Application Information
AI Technical Summary
Problems solved by technology
Method used
Image
Examples
Embodiment 1
[0025] Produce glass fiber composite dough according to the following steps:
[0026] (1) According to the thickness of the carbon fiber composite skin to be produced, prepare one or more pieces of glass fiber cloth, spunlace non-woven fabric made of glass fiber and an appropriate amount of random copolymerized polypropylene and binder, among which, the bonding The mass ratio of agent to random copolymerized polypropylene is 1:6 and the binder includes the following raw materials in parts by mass: 10 parts of phenolic resin, 7 parts of quartz sand, 2 parts of dicyandiamide, 2 parts of dimethylformamide, 1.5 parts of polyacrylate, 3 parts of dipropylene glycol methyl ether, 4 parts of simethicone, 4 parts of fumaric acid, 1.5 parts of fumaric anhydride, 4 parts of trimesic acid, 1.5 parts of trimesic anhydride and anionic surfactant 1.5 parts, the anionic surfactant is the anionic surfactant containing the hydrophobic group shown in the following formula:
[0027]
[0028] ...
Embodiment 2
[0036] Produce glass fiber composite dough according to the following steps:
[0037] (1) According to the thickness of the carbon fiber composite skin to be produced, prepare one or more pieces of glass fiber cloth, spunlace non-woven fabric made of glass fiber and an appropriate amount of random copolymerized polypropylene and binder, among which, the bonding The mass ratio of agent to random copolymerized polypropylene is 1:5 and the binder includes the following raw materials in parts by mass: 10 parts of furan resin, 6 parts of quartz sand, 1 part of dicyandiamide, 1 part of dimethylformamide, 1 part of polyacrylate, 2 parts of dipropylene glycol methyl ether, 3 parts of simethicone, 3 parts of fumaric acid, 1 part of fumaric anhydride, 3 parts of trimesic acid, 1 part of trimesic anhydride and anionic surfactant 1 part, the anionic surfactant is an anionic surfactant containing a hydrophobic group shown in the following formula:
[0038]
[0039] Among them, R 1 is ...
Embodiment 3
[0047] Produce glass fiber composite dough according to the following steps:
[0048](1) According to the thickness of the carbon fiber composite skin to be produced, prepare one or more pieces of glass fiber cloth, spunlace non-woven fabric made of glass fiber and an appropriate amount of random copolymerized polypropylene and binder, among which, the bonding The mass ratio of agent to random copolymerized polypropylene is 1:8 and the binder includes the following raw materials in parts by mass: 10 parts of imide resin, 8 parts of quartz sand, 3 parts of dicyandiamide, 3 parts of dimethylformamide 2 parts, polyacrylate 2 parts, dipropylene glycol methyl ether 4 parts, simethicone 5 parts, fumaric acid 5 parts, fumaric anhydride 2 parts, trimellitic acid 5 parts, trimellitic anhydride 2 parts and anionic surface 2 parts of activator, anionic surfactant is the anionic surfactant containing the hydrophobic group shown in the following formula:
[0049]
[0050] Among them, R...
PUM
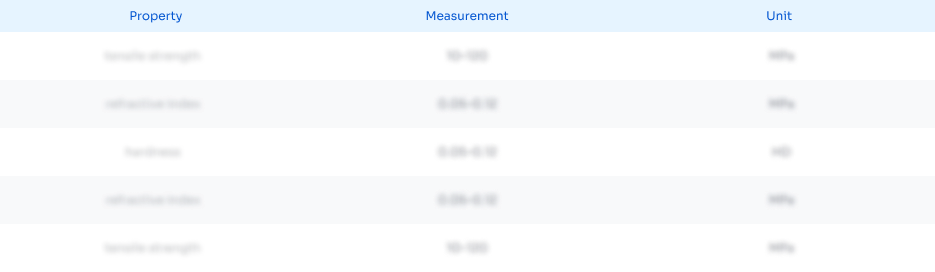
Abstract
Description
Claims
Application Information

- R&D
- Intellectual Property
- Life Sciences
- Materials
- Tech Scout
- Unparalleled Data Quality
- Higher Quality Content
- 60% Fewer Hallucinations
Browse by: Latest US Patents, China's latest patents, Technical Efficacy Thesaurus, Application Domain, Technology Topic, Popular Technical Reports.
© 2025 PatSnap. All rights reserved.Legal|Privacy policy|Modern Slavery Act Transparency Statement|Sitemap|About US| Contact US: help@patsnap.com