Co-sintering molding technology of MIM (metal injection molding) blank and metal product
A technology of metal products and molding process, applied in the field of co-sintering molding process of MIM injection blanks and metal products, can solve the problems of easy splashing around the solder joints, the appearance and quality of film production, poor welding stability, etc. The effect of application prospect, good lasting stability and strong mechanical bearing capacity
- Summary
- Abstract
- Description
- Claims
- Application Information
AI Technical Summary
Problems solved by technology
Method used
Examples
Embodiment 1
[0022] The co-sintering molding process of MIM injection molded blanks and metal products includes the following steps:
[0023] ①Preparation of MIM injection molding: use general process parameters to mix and granulate powder and binder, or directly use commercial powder feeding, injection molding with powder injection molding machine, and take it out from the mold to get MIM injection molding ;
[0024] ② Select metal products: the melting point temperature of the selected metal products should be greater than the maximum sintering temperature of the MIM injection molded blank;
[0025] ③Assembly: Assemble the MIM injection molded blank obtained in step ① with the metal product in step ②. During assembly, it is necessary to ensure that the MIM injection molded blank and the metal product can be assembled directly without using other layout aids;
[0026] ④ Catalytic degreasing: including initial flushing, catalysis, secondary flushing and post-flushing processes, of which ...
Embodiment 2
[0038] The co-sintering molding process of MIM injection molded blanks and metal products includes the following steps:
[0039] ①Preparation of MIM injection molding: use general process parameters to mix and granulate powder and binder, or directly use commercial powder feeding, injection molding with powder injection molding machine, and take it out from the mold to get MIM injection molding ;
[0040] ② Select metal products: the melting point temperature of the selected metal products should be greater than the maximum sintering temperature of the MIM injection molded blank;
[0041] ③Assembly: Assemble the MIM injection molded blank obtained in step ① with the metal product in step ②. During assembly, it is necessary to ensure that the MIM injection molded blank and the metal product can be assembled directly without using other layout aids;
[0042] ④ Catalytic degreasing: including initial flushing, catalysis, secondary flushing and post-flushing processes, of which
...
Embodiment 3
[0054] The co-sintering molding process of MIM injection molded blanks and metal products includes the following steps:
[0055] ①Preparation of MIM injection molding: use general process parameters to mix and granulate powder and binder, or directly use commercial powder feeding, injection molding with powder injection molding machine, and take it out from the mold to get MIM injection molding ;
[0056] ② Select metal products: the melting point temperature of the selected metal products should be greater than the maximum sintering temperature of the MIM injection molded blank;
[0057] ③Assembly: Assemble the MIM injection molded blank obtained in step ① with the metal product in step ②. During assembly, it is necessary to ensure that the MIM injection molded blank and the metal product can be assembled directly without using other layout aids;
[0058] ④ Catalytic degreasing: including initial flushing, catalysis, secondary flushing and post-flushing processes, of which ...
PUM
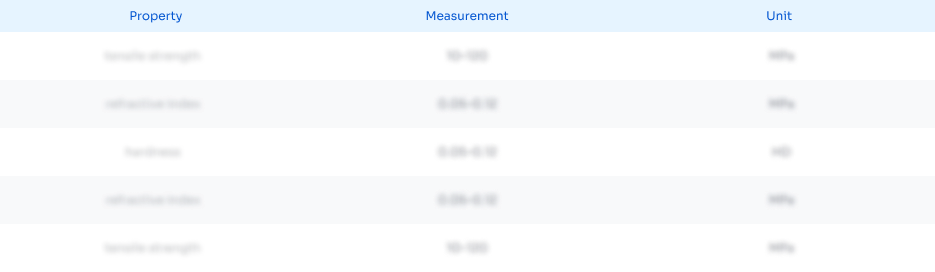
Abstract
Description
Claims
Application Information

- Generate Ideas
- Intellectual Property
- Life Sciences
- Materials
- Tech Scout
- Unparalleled Data Quality
- Higher Quality Content
- 60% Fewer Hallucinations
Browse by: Latest US Patents, China's latest patents, Technical Efficacy Thesaurus, Application Domain, Technology Topic, Popular Technical Reports.
© 2025 PatSnap. All rights reserved.Legal|Privacy policy|Modern Slavery Act Transparency Statement|Sitemap|About US| Contact US: help@patsnap.com