High-strength toughness low-alloy wear-resistant steel and preparation method thereof
A high-strength toughness, low-alloy technology, applied in the field of low-alloy wear-resistant steel, can solve the problems of unguaranteed hardness and insignificant toughness improvement, and achieve the effect of isothermal transformation
- Summary
- Abstract
- Description
- Claims
- Application Information
AI Technical Summary
Problems solved by technology
Method used
Examples
Embodiment 1
[0023] The chemical composition percentage of low alloy wear-resistant steel is: C: 0.52%, Si: 1.20%, Mn: 1.0%, Cr: 0.30%, Mo: 0.20%, Cu: 0.50%, Re: 0.10%, P: 0.025% , S: 0.025%, the rest is Fe and unavoidable impurities.
[0024] Melting with 1t alkaline induction furnace. The metal charge is pig iron for steelmaking, returned carbon steel, ferrosilicon, ferrochrome, ferromolybdenum, scrap copper, rare earth (Re, one or more of all rare earth elements), and the ferroalloy (ferrosilicon, ferrochrome , ferromolybdenum) after being crushed and added, the particle size is 10-20mm, and the feeding is calculated according to the above formula. The lost foam casting is adopted, and the pouring temperature is 1560-1600°C. After the pouring is completed, when the casting is cooled to 800-900°C, the shell is removed and air-cooled to room temperature.
[0025] Then, the casting is heated up to 850°C at a rate of 4°C per minute in the heating equipment for austenitization, and then th...
Embodiment 2
[0028] The chemical composition percentage of low alloy wear-resistant steel is: C: 0.4%, Si: 0.6%, Mn: 0.3%, Cr: 0.25%, Mo: 0.15%, Cu: 0.40%, Re: 0.10%, P: 0% , S: 0%, the rest is Fe and unavoidable impurities.
[0029] Melting with 1t alkaline induction furnace. The metal charge is pig iron for steelmaking, returned carbon steel, ferrosilicon, ferrochrome, ferromolybdenum, scrap copper, rare earth (Re, one or more of all rare earth elements), and the ferroalloy (ferrosilicon, ferrochrome , ferromolybdenum) after being crushed and added, the particle size is 10-20mm, and the feeding is calculated according to the above formula. The lost foam casting is adopted, and the pouring temperature is 1560-1600°C. After the pouring is completed, when the casting is cooled to 800-900°C, the shell is removed and air-cooled to room temperature.
[0030] Then, the casting is heated up to 820°C at a rate of 2°C per minute in the heating equipment for austenitization, and then the casting ...
PUM
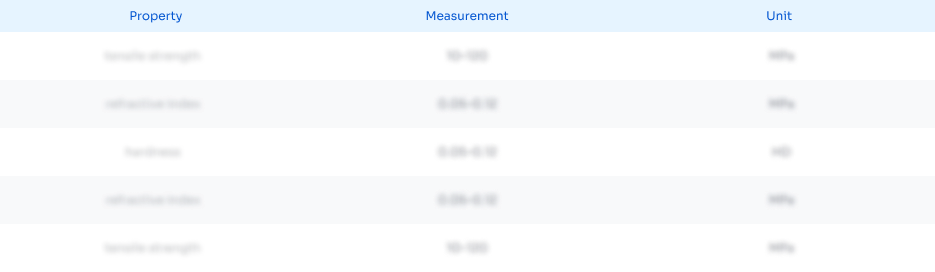
Abstract
Description
Claims
Application Information

- Generate Ideas
- Intellectual Property
- Life Sciences
- Materials
- Tech Scout
- Unparalleled Data Quality
- Higher Quality Content
- 60% Fewer Hallucinations
Browse by: Latest US Patents, China's latest patents, Technical Efficacy Thesaurus, Application Domain, Technology Topic, Popular Technical Reports.
© 2025 PatSnap. All rights reserved.Legal|Privacy policy|Modern Slavery Act Transparency Statement|Sitemap|About US| Contact US: help@patsnap.com