Metal sulfide ceramic friction material and preparation method thereof
A metal sulfide and friction material technology, applied in the field of friction materials, can solve the problems of complex production process, high production cost, and low thermal stability of asbestos friction materials, and achieves good running-in performance, convenient operation and easy operation. The effect of industrial production
- Summary
- Abstract
- Description
- Claims
- Application Information
AI Technical Summary
Problems solved by technology
Method used
Image
Examples
Embodiment 1
[0024] Step 1. Weigh respectively according to weight percentage: 1g of sulfur powder, 11g of tin powder, 10g of antimony trisulfide, 5g of alumina powder, 40g of iron and aluminum powder, 25g of steel fiber, 3g of molybdenum disulfide, and 5g of graphite;
[0025] Step 2. Mix the sulfur powder, tin powder, antimony trisulfide, alumina powder and iron-aluminum powder weighed in step 1, put them into a ball mill and mill them for 2 hours, take them out, add the steel fiber and disulfide disulfide weighed in step 1 Molybdenum, graphite, stir to make it evenly mixed;
[0026] Step 3. Add a molding agent to the raw material obtained in step 2, stir evenly, dry press molding on a tablet machine at a molding pressure of 280 MPa, and then dry at 80°C for 2 hours;
[0027] Step 4. After burying the raw material obtained in Step 3 with carbon powder, put it into a thyristor high-temperature furnace for normal-pressure sintering at 450° C., and cool naturally to obtain the finished prod...
Embodiment 2
[0029] Step 1. Weigh respectively according to weight percentage: 5g of sulfur powder, 3g of tin powder, 20g of antimony trisulfide, 9g of alumina powder, 30g of iron and aluminum powder, 28g of steel fiber, 2g of molybdenum disulfide, and 3g of graphite;
[0030] Step 2. Mix the sulfur powder, tin powder, antimony trisulfide, alumina powder and iron-aluminum powder weighed in step 1, put them into a ball mill and mill them for 2h to 3h, take them out, add the steel fiber weighed in step 1, Molybdenum disulfide, graphite, stir to make it evenly mixed;
[0031] Step 3. Add a molding agent to the raw material obtained in step 2, stir evenly, dry press molding on a tablet machine at a molding pressure of 360 MPa, and then dry at 60°C for 3 hours;
[0032] Step 4. After burying the raw material obtained in Step 3 with carbon powder, put it into a thyristor high-temperature furnace for normal pressure sintering at a temperature of 600° C., and cool naturally to obtain the finished ...
Embodiment 3
[0034] Step 1. Weigh respectively according to weight percentage: 3g of sulfur powder, 7g of tin powder, 15g of antimony trisulfide, 5g of alumina powder, 35g of iron and aluminum powder, 30g of steel fiber, 2g of molybdenum disulfide, and 3g of graphite;
[0035] Step 2. Mix the sulfur powder, tin powder, antimony trisulfide, alumina powder and iron-aluminum powder weighed in step 1, put them into a ball mill and mill them for 2 hours, take them out, add the steel fiber and disulfide disulfide weighed in step 1 Molybdenum, graphite, stir to make it evenly mixed;
[0036] Step 3. Add a molding agent to the raw material obtained in step 2, stir evenly, dry press molding on a tablet machine at a molding pressure of 320 MPa, and then dry at a temperature of 70°C for 3 hours;
[0037] Step 4. After burying the raw material obtained in Step 3 with carbon powder, put it into a thyristor high-temperature furnace for normal-pressure sintering at a temperature of 500° C., and cool natu...
PUM
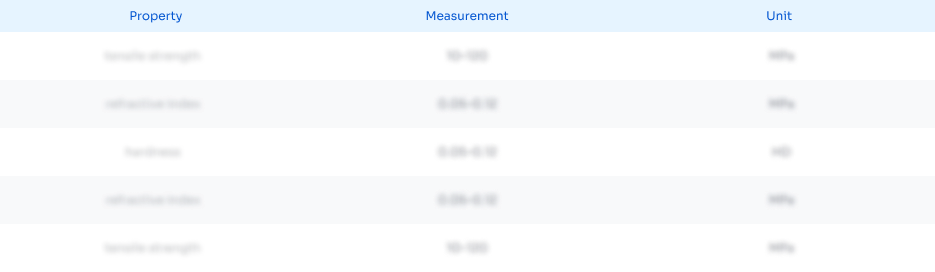
Abstract
Description
Claims
Application Information

- R&D Engineer
- R&D Manager
- IP Professional
- Industry Leading Data Capabilities
- Powerful AI technology
- Patent DNA Extraction
Browse by: Latest US Patents, China's latest patents, Technical Efficacy Thesaurus, Application Domain, Technology Topic, Popular Technical Reports.
© 2024 PatSnap. All rights reserved.Legal|Privacy policy|Modern Slavery Act Transparency Statement|Sitemap|About US| Contact US: help@patsnap.com