Treatment process for copper smelting smoke dust
A treatment process, copper smelting technology, applied in the field of copper smelting fume treatment process, can solve problems such as difficult to handle, reduce conversion rate, pollute the environment, etc., achieve the effect of improving capacity and solving open circuit problems
- Summary
- Abstract
- Description
- Claims
- Application Information
AI Technical Summary
Problems solved by technology
Method used
Image
Examples
Embodiment 1
[0079] See Table 1-1 for the composition of copper smelting dust, which contains high arsenic and low copper; see Table 1-2 for the composition of waste acid.
[0080] Table 1-1 Composition of copper smelting dust
[0081] Element As Cu Fe Pb Zn Sb Bi content % % % % % % % soot 9.883 8.390 12.249 5.366 2.962 0.099 0.493
[0082] Table 1-2 Composition of waste acid
[0083] As Cu Fe Pb Zn Sb Bi h 2 SO 4 g / L g / L g / L g / L g / L g / L g / L g / L 0.32 0.1 0.099 0.0098 0.023 0.003 0.003 186
[0084] 1. Pickling
[0085] Prepare the waste acid into an acid solution with an acid mass concentration of 12.5%, and prepare the solution according to the solid-to-liquid ratio of smoke and acid solution at a ratio of 1:4, add it to the reaction kettle, heat it to 80°C, and react for 3.5 hours. After 3.5 hours, it will be solid-liquid Separation and leaching results are shown in Table 1...
Embodiment 2
[0119] The composition of copper smelting dust is shown in Table 2-1, and the dust contains high arsenic and low copper; the composition of waste acid is shown in Table 2-2.
[0120] Table 2-1 Composition of copper smelting dust
[0121] Element As Cu Fe Pb Zn Sb Bi content % % % % % % % soot 20.035 9.125 13.351 2.281 3.621 0.121 0.651
[0122] Table 2-2 Composition of waste acid
[0123] As Cu Fe Pb Zn Sb Bi h 2 SO 4 g / L g / L g / L g / L g / L g / L g / L g / L 0.12 0.105 0.086 0.001 0.035 0.004 0.004 136
[0124] 1. Pickling
[0125] Prepare the waste acid so that the acid concentration is 165g / l, make liquid according to the solid-to-liquid ratio of dust and acid liquid mass 1:6, add it to the reaction kettle, heat to 70°C, react for 5 hours, and separate the solid and liquid after 5 hours, see the leaching results Table 2-3.
[0126] Table 2-3 Leaching results
[0127] ...
Embodiment 3
[0160] The composition of copper smelting dust is shown in Table 3-1, the dust contains high arsenic and low copper; the composition of waste acid is shown in Table 3-2.
[0161] Table 3-1 Composition of copper smelting dust
[0162] Element As Cu Fe Pb Zn Sb Bi content % % % % % % % soot 15.314 7.951 11.382 4.655 4.210 0.101 0.750
[0163] Table 3-2 Composition of waste acid
[0164] As Cu Fe Pb Zn Sb Bi h 2 SO 4 g / L g / L g / L g / L g / L g / L g / L g / L 0.510 0.135 0.132 0.013 0.041 0.003 0.004 170
[0165] 1. Pickling
[0166] Prepare the waste acid into an acid solution with an acid mass concentration of 130g / l, and prepare the solution according to the solid-to-liquid ratio of smoke dust and acid solution at a ratio of 1:4.5, add it to the reaction kettle, heat to 80°C, and react for 3.5 hours. After 3.5 hours, it will solidify Liquid separation, leaching results are ...
PUM
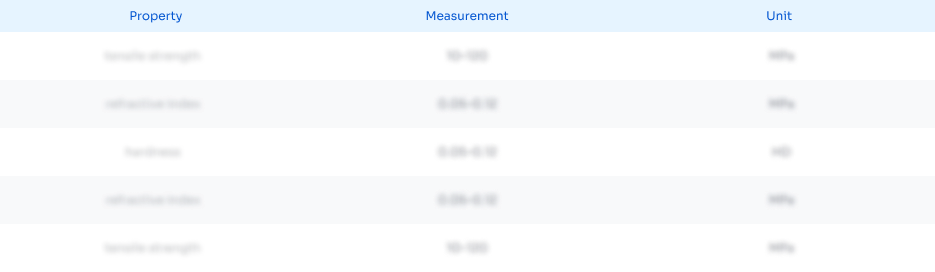
Abstract
Description
Claims
Application Information

- R&D Engineer
- R&D Manager
- IP Professional
- Industry Leading Data Capabilities
- Powerful AI technology
- Patent DNA Extraction
Browse by: Latest US Patents, China's latest patents, Technical Efficacy Thesaurus, Application Domain, Technology Topic, Popular Technical Reports.
© 2024 PatSnap. All rights reserved.Legal|Privacy policy|Modern Slavery Act Transparency Statement|Sitemap|About US| Contact US: help@patsnap.com