Purification process of electroplating waste liquid
A technology for electroplating waste liquid and process, which is applied in the field of purification process of electroplating waste liquid, can solve the problems that the quality of the electroplating layer is greatly affected, hinder the recycling of waste chromic anhydride, etc., so as to save the cost of raw materials and pollutant treatment costs, reduce external The effect of pollution
- Summary
- Abstract
- Description
- Claims
- Application Information
AI Technical Summary
Problems solved by technology
Method used
Image
Examples
Embodiment 1
[0053] Chromic anhydride content: 262g / kg, sulfate ion content: 4.1g / kg, trivalent chromium ion content: 3.6g / kg, copper ion content: 1.79g / kg, iron ion content: 5.84g / kg, zinc ion Content: 1.25g / kg, chloride ion content: 9.9g / kg electroplating waste liquid at room temperature, after hydrogen peroxide oxidation and activated carbon filtration, and then through the pressure pump at a pressure of 0.2MPa, into the first filter for the second One time filtration, the filtration flow rate is 400L / h, the filtration flow rate is maintained, and the second filtration is performed through the second filter to obtain the filtered electroplating waste liquid.
[0054] Maintain the filtration flow rate. After the filtered electroplating waste liquid obtained in the above steps is adsorbed by the first resin column filled with 45% sulfonic acid group cation exchange resin and 55% amino anion exchange resin, a treatment waste liquid is obtained; Then the first-stage treatment waste liquid obta...
Embodiment 2
[0063] Chromic anhydride content: 404g / kg, sulfate ion content: 3.3g / kg, trivalent chromium ion content: 4.0g / kg, copper ion content: 2.31g / kg, iron ion content: 6.35g / kg, zinc ion Content: 2.02g / kg, chloride ion content: 4.9g / kg electroplating waste liquid at room temperature, after hydrogen peroxide oxidation and activated carbon filtration, and then through the pressure pump at a pressure of 0.4MPa, into the first filter for the second One time filtration, the filtration flow rate is 600L / h, the filtration flow rate is maintained, and the second filtration is performed through the second filter to obtain the filtered electroplating waste liquid.
[0064] Maintain the filtration flow rate. After the filtered electroplating waste liquid obtained in the above steps is adsorbed by the first resin column filled with 43% sulfonic acid group cation exchange resin and 54% amino anion exchange resin, a treatment waste liquid is obtained; maintain the flow rate Then the first-stage trea...
Embodiment 3
[0067] Chromic anhydride content: 520g / kg, sulfate ion content: 3.6g / kg, trivalent chromium ion content: 5.0g / kg, copper ion content: 2.81g / kg, iron ion content: 7.35g / kg, zinc ion Content: 2.52g / kg, chloride ion content: 13.7g / kg electroplating waste liquid at room temperature, after hydrogen peroxide oxidation and activated carbon filtration, and then through the pressure pump at a pressure of 0.6MPa, into the first filter for the second One time filtration, the filtration flow rate is 750L / h, the filtration flow rate is maintained, and the second filtration is performed through the second filter to obtain the filtered electroplating waste liquid.
[0068] Maintain the filtration flow rate. After the filtered electroplating waste liquid obtained in the above steps is adsorbed by the first resin column filled with 40% sulfonic acid group cation exchange resin and 55% amino anion exchange resin, a treatment waste liquid is obtained; Then the first-stage treatment waste liquid obt...
PUM
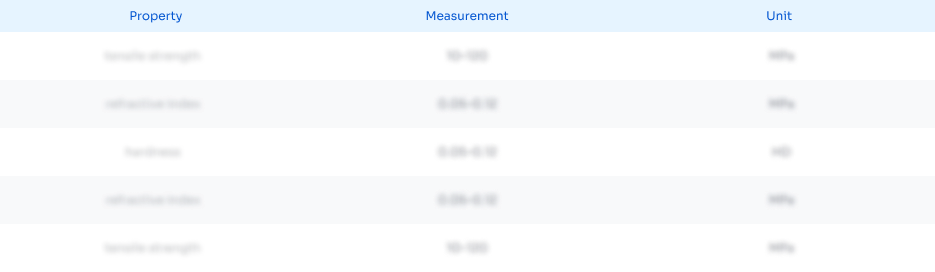
Abstract
Description
Claims
Application Information

- R&D Engineer
- R&D Manager
- IP Professional
- Industry Leading Data Capabilities
- Powerful AI technology
- Patent DNA Extraction
Browse by: Latest US Patents, China's latest patents, Technical Efficacy Thesaurus, Application Domain, Technology Topic, Popular Technical Reports.
© 2024 PatSnap. All rights reserved.Legal|Privacy policy|Modern Slavery Act Transparency Statement|Sitemap|About US| Contact US: help@patsnap.com