Heat treatment process capable of improving NDT performance of steel for F-grade ultrahigh-strength ocean platform
An offshore platform, ultra-high-strength technology, applied in the field of heat treatment technology, can solve the problems that have not been mentioned about the impact of NDT performance, and achieve the effects of avoiding coarse lath martensite structure, improving NDT performance, and suppressing stress concentration
- Summary
- Abstract
- Description
- Claims
- Application Information
AI Technical Summary
Problems solved by technology
Method used
Examples
Embodiment 1
[0025] In this embodiment, a heat treatment process for improving the NDT performance of F-grade ultra-high-strength offshore platform steel adopts F-grade offshore platform steel with a plate thickness of 115 mm, which is rolled from a 420 mm thick cast slab.
[0026] This embodiment adopts the online quenching + high temperature sub-temperature quenching + tempering heat treatment process, that is, the online quenching temperature is Ac3+(80~100)°C, the final cooling temperature is ≤300°C, online ultra-fast cooling is adopted, and the average cooling rate is 20~50°C / s; high temperature sub-temperature quenching temperature is Ac3? (5~10) ℃, holding time is 1.4~1.8min / mm, using high-pressure water cooling, final cooling temperature ≤ 100 ℃, average cooling rate ≥ 20 ℃ / s; The tempering temperature is Ac1?(50~80)℃, and the holding time is 2.0~3.5min / mm. On-line quenching is carried out in the ultra-fast cooling device after rolling and completed in water cooling; high-temperat...
Embodiment 2
[0028] This embodiment is a heat treatment process for improving the NDT performance of F-grade ultra-high-strength offshore platform steel. The F-grade offshore platform steel used has a plate thickness of 115mm and is rolled from a 420mm thick cast slab.
[0029]On-line quenching + high temperature sub-temperature quenching + tempering heat treatment process is adopted, that is, the on-line quenching temperature is Ac3+(50~70) ℃, the final cooling temperature is ≤100 ℃, online ultra-fast cooling is adopted, and the average cooling rate is 15~40 ℃ / s; The high-temperature sub-temperature quenching temperature is Ac3?(10~20)℃, the holding time is 1.4-1.8min / mm, high-pressure water cooling is used, the final cooling temperature is ≤100℃, and the average cooling rate is ≥20℃ / s; the tempering temperature is Ac1?(100~150)℃, the holding time is 2.5-4.0min / mm. On-line quenching is carried out in the ultra-fast cooling device after rolling and completed in water cooling; high-temperat...
Embodiment 3
[0031] This embodiment is a heat treatment process for improving the NDT performance of F-grade ultra-high-strength offshore platform steel. The F-grade offshore platform steel used has a plate thickness of 115mm and is rolled from a 420mm thick cast slab.
[0032] Adopt online quenching + high temperature sub-temperature quenching + tempering heat treatment process, that is, the online quenching temperature is Ac3+(60~90)℃, the final cooling temperature is ≤300℃, online ultra-fast cooling is adopted, and the average cooling rate is 15~30℃ / s; The high-temperature sub-temperature quenching temperature is Ac3?(5~15)℃, the holding time is 1.5~2.0min / mm, high-pressure water cooling is used, the final cooling temperature is ≤50℃, and the average cooling rate is ≥25℃ / s; the tempering temperature is Ac1?(50~120)℃, holding time is 2.5~4.0min / mm. Quenching heating is carried out in the normalizing furnace, completed in the process of water cooling, and tempering heating is carried out ...
PUM
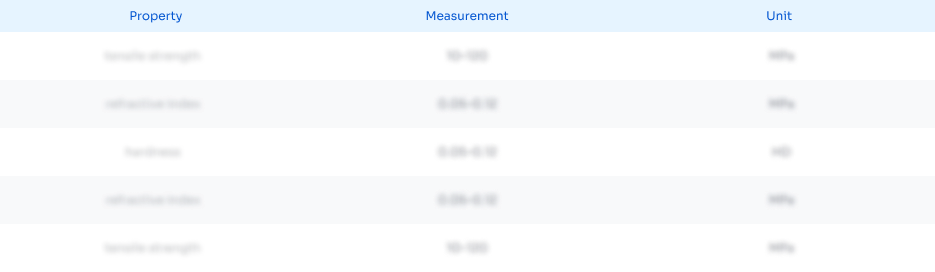
Abstract
Description
Claims
Application Information

- R&D Engineer
- R&D Manager
- IP Professional
- Industry Leading Data Capabilities
- Powerful AI technology
- Patent DNA Extraction
Browse by: Latest US Patents, China's latest patents, Technical Efficacy Thesaurus, Application Domain, Technology Topic, Popular Technical Reports.
© 2024 PatSnap. All rights reserved.Legal|Privacy policy|Modern Slavery Act Transparency Statement|Sitemap|About US| Contact US: help@patsnap.com