Highly-hydrophilic colored contact lens material preparation method
A contact lens, high hydrophilic technology, applied in glasses/goggles, instruments, optics, etc., can solve the problems of inability to achieve mass production, uneven lens surface, foreign body sensation when patients wear it, etc., to achieve tensile strength Large, high moisture content, the effect of improving light transmittance
- Summary
- Abstract
- Description
- Claims
- Application Information
AI Technical Summary
Problems solved by technology
Method used
Examples
Embodiment 1
[0016] (1) Mixing of raw materials: Take 30g of N vinylpyrrolidone and B hydroxyethyl methacrylate with a mass ratio of 1:1 in a round bottom flask, and add transparent blue 7.20×10 -4g As a coloring material, add 0.2 g of benzoin diethyl ether as an initiator, stir magnetically for 0.5 h, and mix the components uniformly to obtain a solution;
[0017] (2) Mold forming: filter the solution prepared in step (1) under dust-free operation, draw quantitative filtrate with a pipette, drop it into a self-made glass mold, and cover the upper layer of the mold with a transparent quartz glass plate.
[0018] (3) Curing synthesis: Intermittently irradiate the filtrate in the glass mold in step (2) with an ultraviolet lamp, wherein the time interval for the irradiation of the ultraviolet lamp is 2s. After the liquid is cured, turn off the ultraviolet lamp and let it stand at room temperature 25°C 0.8h.
[0019] (4) Soaking and cleaning: After standing still, remove the quartz glass, and...
Embodiment 2
[0020] Example 2: The rest are the same as in Example 1, except that in the step (1), the amount of transparent blue material added is 7.30×10 -4 g, the addition amount of benzoin ether is 0.3g, and the magnetic stirring time is 0.4h; in the step (3), the standing time is 0.9h; in the step (4), the soaking time is 23h.
Embodiment 3
[0021] Example 3: The rest are the same as in Example 1, except that in the step (1), the amount of transparent blue material added is 7.38×10 -4 g, the addition amount of benzoin ether is 0.4g, and the magnetic stirring time is 0.5h; in the step (3), the standing time is 1.0h; in the step (4), the soaking time is 24h.
[0022] After the above process steps, the lens material samples are taken out to be tested:
[0023] serial number Transmittance / % Tensile strength / Pa Moisture content / % PH value of sample leach solution Example 1 98 920 68 7.06 Example 2 97 916 70 7.12 Example 3 97 918 71 7.13
[0024] From the above data, it can be known that the produced lens material samples have high light transmittance of over 96%, high tensile strength, not easy to damage, moisture content of over 65%, good wearing comfort, and the pH value of the sample leachate is 7.06-7.13 , which is close to the pH7.2 of human tears, the process ...
PUM
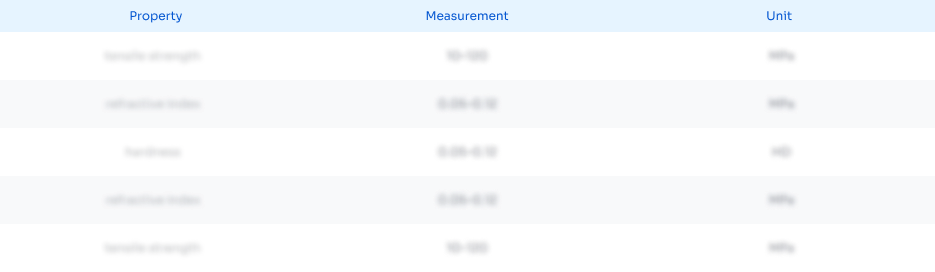
Abstract
Description
Claims
Application Information

- R&D
- Intellectual Property
- Life Sciences
- Materials
- Tech Scout
- Unparalleled Data Quality
- Higher Quality Content
- 60% Fewer Hallucinations
Browse by: Latest US Patents, China's latest patents, Technical Efficacy Thesaurus, Application Domain, Technology Topic, Popular Technical Reports.
© 2025 PatSnap. All rights reserved.Legal|Privacy policy|Modern Slavery Act Transparency Statement|Sitemap|About US| Contact US: help@patsnap.com