Method for efficient preparation of biomass based aromatic hydrocarbon
A technology based on biomass and aromatics, applied in chemical instruments and methods, hydrocarbon production from oxygen-containing organic compounds, bulk chemical production, etc., can solve the problems of long reaction steps, low yield of aromatics, low energy consumption, etc.
- Summary
- Abstract
- Description
- Claims
- Application Information
AI Technical Summary
Problems solved by technology
Method used
Image
Examples
Embodiment 1
[0022] Weigh 35 grams of ZSM-5 with a silicon-aluminum ratio of 25 and mix it with 35 grams of γ-alumina additive, add 2.7 grams of scallop powder, and mix well. Then add 48 grams of nitric acid aqueous solution with a mass percentage of nitric acid of 5.5%, knead and shape, and extrude. The obtained catalyst precursor was dried at 120° C. for 8 hours and calcined at 500° C. for 2 hours to obtain a molecular sieve catalyst. Catalyst activity evaluation is carried out on a fixed bed, the reaction conditions are 3 grams of catalyst mass, 2,5-dimethylfuran as the reaction substrate, and 1.0 hour weight space velocity -1 , hydrogen pressure 1.0MPa, flow 50mlmin -1 , temperature 400°C. After the reaction, the conversion rate of the reaction substrate was 49%, and the selectivity of BTX was 66%.
Embodiment 2
[0024] Weigh 35 grams of Y molecular sieve with a silicon-aluminum ratio of 6 and mix with 35 grams of γ-alumina additive, add 2.7 grams of scallop powder, and mix well. Then add 48 grams of nitric acid aqueous solution with a mass percentage of nitric acid of 5.5%, knead and shape, and extrude. The obtained catalyst precursor was dried at 120° C. for 8 hours and calcined at 500° C. for 2 hours to obtain a molecular sieve catalyst. Catalyst activity evaluation is carried out on a fixed bed, the reaction conditions are 3 grams of catalyst mass, 2,5-dimethylfuran as the reaction substrate, and 1.0 hour weight space velocity -1 , hydrogen pressure 1.0MPa, flow 50mlmin -1 , temperature 400°C. After the reaction, the conversion rate of the reaction substrate was 44%, and the selectivity of BTX was 62%.
Embodiment 3
[0026] Weigh 35 grams of beta molecular sieve with a silicon-aluminum ratio of 30 and mix with 35 grams of γ-alumina additive, add 2.7 grams of scallop powder, and mix well. Then add 48 grams of nitric acid aqueous solution with a mass percentage of nitric acid of 5.5%, knead and shape, and extrude. The obtained catalyst precursor was dried at 120° C. for 8 hours and calcined at 500° C. for 2 hours to obtain a molecular sieve catalyst. Catalyst activity evaluation is carried out on a fixed bed, the reaction conditions are 3 grams of catalyst mass, 2,5-dimethylfuran as the reaction substrate, and 1.0 hour weight space velocity -1 , hydrogen pressure 1.0MPa, flow 50mlmin -1 , temperature 400°C. After the reaction, the conversion rate of the reaction substrate was 46%, and the selectivity of BTX was 56%.
PUM
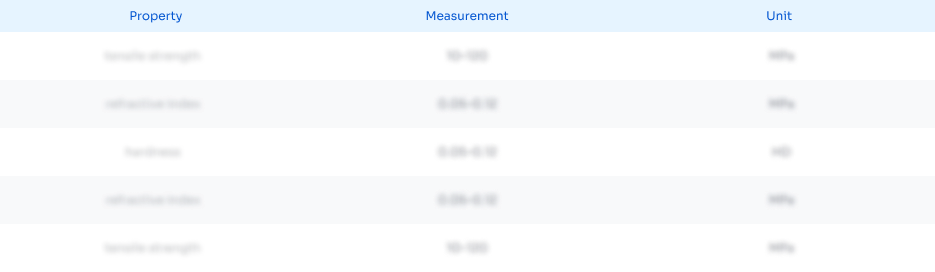
Abstract
Description
Claims
Application Information

- R&D
- Intellectual Property
- Life Sciences
- Materials
- Tech Scout
- Unparalleled Data Quality
- Higher Quality Content
- 60% Fewer Hallucinations
Browse by: Latest US Patents, China's latest patents, Technical Efficacy Thesaurus, Application Domain, Technology Topic, Popular Technical Reports.
© 2025 PatSnap. All rights reserved.Legal|Privacy policy|Modern Slavery Act Transparency Statement|Sitemap|About US| Contact US: help@patsnap.com