Reactive phosphorus flame retardant and preparation method thereof
A phosphorus-based flame retardant and reactive technology, which is applied in the field of reactive phosphorus-based flame retardants and their preparation, can solve the problem of less halogen-free flame retardants, and achieve the effects of improved toughness, high purity, and easy control
- Summary
- Abstract
- Description
- Claims
- Application Information
AI Technical Summary
Problems solved by technology
Method used
Image
Examples
Embodiment 1
[0027] Step 1: Add PEPA16.24g and phosphorus oxychloride 5ml into a 250ml three-necked flask equipped with a reflux condenser, a thermometer and a magnet, then add 50ml of acetonitrile as a solvent, and raise the reaction temperature until the temperature rises to 80°C. The catalyst DMAP is added, and the reaction temperature is controlled between 80-82°C. After continuing the reaction for 25 hours, a white solid precipitates out. After the product is washed with acetone or acetonitrile, the white powder obtained after drying at 60°C is the intermediate.
[0028] Step 2: Add 2.63g of intermediates and 1.53g of polyethylene glycol to a 100ml three-necked flask equipped with a reflux condenser, thermometer and magnet, and then add 40ml of acetonitrile as a solvent. After the temperature rises to 80°C, add 0.1g of DMAP In the three-necked flask, control the temperature at 80-82°C for reaction. After 25 hours of reaction time, the temperature was lowered to room temperature, and a...
Embodiment 2
[0031] The first step: the synthesis method of a reactive phosphorus-based flame retardant intermediate is the same as in Example 1.
[0032] Step 2: Add 2.60g of intermediates and 1.7g of polyethylene glycol to a 100ml three-necked flask equipped with a reflux condenser, thermometer and magnet, and then add 25ml of DMSO as a solvent. After the temperature rises to 80°C, add an acid-binding agent: 0.52g pyridine; then add catalyst: 0.1g DMAP was added into the three-necked flask, and the temperature was controlled to react at 80-82°C. After 20 hours of reaction time, it was lowered to room temperature to obtain a yellow solution and a precipitate, which were suction filtered, washed and dried to obtain a white solid powder.
[0033] Step 3: Step 3: Add 4.31g of polymer and 0.75g of epichlorohydrin to a 100ml three-necked flask equipped with a magnetic stirrer, a thermometer and a magnet. After heating up to 90°C, add 0.1g of DMAP and 0.50g of pyridine Add it into a three-neck...
Embodiment 3
[0035] The first step: the synthesis method of a reactive phosphorus-based flame retardant intermediate is the same as in Example 1.
[0036] Step 2: Add 2.55g of intermediates and 1.8g of polyethylene glycol to a 100ml three-necked flask equipped with a reflux condenser, thermometer and magnet, and then add 30ml of DMSO as a solvent. After the temperature rises to 90°C, add an acid-binding agent: 0.71g triethylamine; then add catalyst: 0.1g DMAP is added into the three-necked flask, and the temperature is controlled at 90-95°C for reaction. After 25 hours of reaction time, it was lowered to room temperature to obtain a yellow solution and a precipitate, which were suction filtered, washed and dried to obtain a white solid powder.
[0037] Step 3: Add 4g of polymer and 0.8g of epichlorohydrin to a 100ml three-necked flask equipped with a magnetic stirrer, a thermometer and a magnet. After the temperature rises to 90°C, add 0.1g of DMAP and 0.72g of triethylamine to the three-n...
PUM
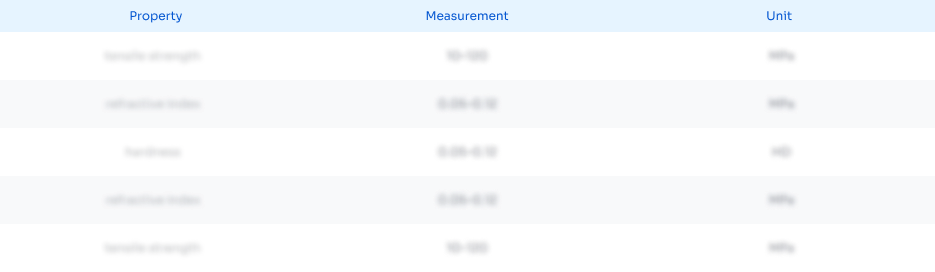
Abstract
Description
Claims
Application Information

- Generate Ideas
- Intellectual Property
- Life Sciences
- Materials
- Tech Scout
- Unparalleled Data Quality
- Higher Quality Content
- 60% Fewer Hallucinations
Browse by: Latest US Patents, China's latest patents, Technical Efficacy Thesaurus, Application Domain, Technology Topic, Popular Technical Reports.
© 2025 PatSnap. All rights reserved.Legal|Privacy policy|Modern Slavery Act Transparency Statement|Sitemap|About US| Contact US: help@patsnap.com