Method for producing aqueous polyurethane synthetic leather
A water-based polyurethane and manufacturing method technology, applied in the field of synthetic leather, can solve the problems of difficult to meet ecological synthetic leather, threat, solvent residue, etc., and achieve the effect of good hand feeling and mechanical properties
- Summary
- Abstract
- Description
- Claims
- Application Information
AI Technical Summary
Problems solved by technology
Method used
Examples
Embodiment 1
[0023] A kind of manufacture method of waterborne polyurethane synthetic leather, comprises the following steps:
[0024] (1) In parts by weight, 1 part of calcium formate and 2 parts of calcium chloride are dissolved in 80 parts of water to make a treatment solution, stirred evenly and packed into a dipping tank, the base cloth is soaked in the treatment solution through the dipping tank, Then pass through rollers, the impregnation amount is 90% of the weight of the base cloth, and then dry in an oven at 100° C. to obtain a pretreated base cloth.
[0025] (2) In parts by weight, 5 parts of ammonium carbonate and 2.5 parts of ammonium nitrate were dissolved in 100 parts of water to obtain a foaming coagulant.
[0026] In parts by weight, 8 parts of foaming coagulant, 9 parts of calcium carbonate and 1 part of pigment are added to 100 parts of water-based polyurethane, and the mixture is evenly mixed to obtain water-based polyurethane slurry; wherein, water-based polyurethane i...
Embodiment 2
[0030] A kind of manufacture method of waterborne polyurethane synthetic leather, comprises the following steps:
[0031] (1) In parts by weight, 2 parts of calcium formate and 1 part of calcium chloride are dissolved in 90 parts of water to make a treatment solution, stirred evenly and packed into a dipping tank, the base cloth is soaked in the treatment solution through the dipping tank, Then pass through rollers, the impregnation amount is 80% of the weight of the base cloth, and then dry in an oven at 120° C. to obtain a pretreated base cloth.
[0032] (2) In parts by weight, 2 parts of ammonium carbonate and 3 parts of ammonium nitrate were dissolved with 85 parts of water to obtain a foaming coagulant.
[0033] In parts by weight, 9 parts of foam coagulant, 8 parts of calcium carbonate and 2 parts of pigment are added to 100 parts of water-based polyurethane, and mixed uniformly to obtain water-based polyurethane slurry; wherein, water-based polyurethane is a product of ...
Embodiment 3
[0037] A kind of manufacture method of waterborne polyurethane synthetic leather, comprises the following steps:
[0038] (1) In parts by weight, 2 parts of calcium formate and 1.5 parts of calcium chloride are dissolved in 100 parts of water to make a treatment solution, stirred evenly and packed into a dipping tank, the base cloth is soaked in the treatment solution through the dipping tank, Then pass through rollers, the impregnation amount is 70% of the weight of the base cloth, and then dry in an oven at 110° C. to obtain a pretreated base cloth.
[0039] (2) In parts by weight, 3 parts of ammonium carbonate and 2 parts of ammonium nitrate were dissolved in 80 parts of water to obtain a foaming coagulant.
[0040] In parts by weight, 10 parts of foaming coagulant, 6 parts of calcium carbonate and 1.5 parts of pigment are added to 100 parts of water-based polyurethane with a solid content of 30%, and mixed uniformly to obtain water-based polyurethane slurry.
[0041] (3) ...
PUM
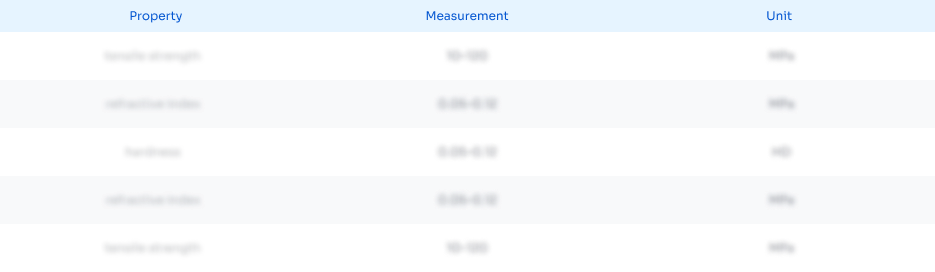
Abstract
Description
Claims
Application Information

- R&D
- Intellectual Property
- Life Sciences
- Materials
- Tech Scout
- Unparalleled Data Quality
- Higher Quality Content
- 60% Fewer Hallucinations
Browse by: Latest US Patents, China's latest patents, Technical Efficacy Thesaurus, Application Domain, Technology Topic, Popular Technical Reports.
© 2025 PatSnap. All rights reserved.Legal|Privacy policy|Modern Slavery Act Transparency Statement|Sitemap|About US| Contact US: help@patsnap.com