Method for preparing buffer material from plant straws
A technology of plant straw and buffer material, applied in the field of buffer material, can solve the problems of inability to guarantee green environmental protection, poor recovery, poor strength, etc., and achieve the effects of low cost of raw materials, good buffer performance, and simple production process method.
- Summary
- Abstract
- Description
- Claims
- Application Information
AI Technical Summary
Problems solved by technology
Method used
Examples
Embodiment 1
[0059] Example 1: Mix the coarsely crushed wheat crop stalks and the finely crushed wood scraps at a weight ratio of 90:10 to form a solid mixed powder; the solid mixed powder is mixed with water in proportion and then sterilized as a culture medium. The weight ratio of mixed powder to water is 80:20, heat the mixed medium to 200°C for sterilization; in the sterile space, the temperature is 15°C, the relative air humidity is 95%, the medium is put into the mold, Inoculate the culture medium with liquid strains and cultivate for 10 days; after the mycelium is overgrown and the fruiting body grows to form the surface layer of the fruiting body, dry the medium at 40°C to keep the water content at 5%. In between, the dried culture medium is peeled off from the mold, which is the buffer material.
Embodiment 2
[0060] Embodiment 2: the mixture of coarsely crushed indica rice crop stalks, rye crop stalks, corn crop stalks, soybean crop stalks, sweet potato crop stalks and finely crushed wheat bran and rice The mixture of shell powder is mixed into solid mixed powder at a weight ratio of 10:90; the solid mixed powder is mixed with water in proportion and then sterilized as a culture medium, and the weight ratio of solid mixed powder to water is 50:50. The good medium is heated to 80°C for sterilization; in the sterile space, the temperature is 25°C, and the relative humidity of the air is 70%. Put the medium into the mold, inoculate the medium with liquid bacteria, and cultivate it for 6 days; After the silk grows and grows fruiting bodies to form the surface layer of fruiting bodies, dry the culture medium at a temperature of 100°C to retain 10% of the water in it. After drying, the culture medium is peeled off from the mold, which is the buffer material .
Embodiment 3
[0061] Embodiment 3: the rapeseed stalk crop stalk crushed powder of coarse crushed powder, the shavings crushed powder mixture and the wheat bran powder of finely crushed powder are mixed into solid mixed powder in a weight ratio of 60:40; solid mixed powder and water are mixed in proportion Mix and sterilize as a medium, the weight ratio of solid mixed powder to water is 70:30, heat the mixed medium to 120°C for sterilization; in the sterile space, the temperature is 35°C, and the relative air humidity is 75%. Put the culture medium into the mold, inoculate the culture medium with liquid strains, and cultivate for 3 days; after the mycelium is full and the fruiting body grows to form the surface layer of the fruiting body, the medium is dried at a temperature of 150°C. Keep the water content at 20%, and peel off the dried medium from the mold, which is the buffer material.
PUM
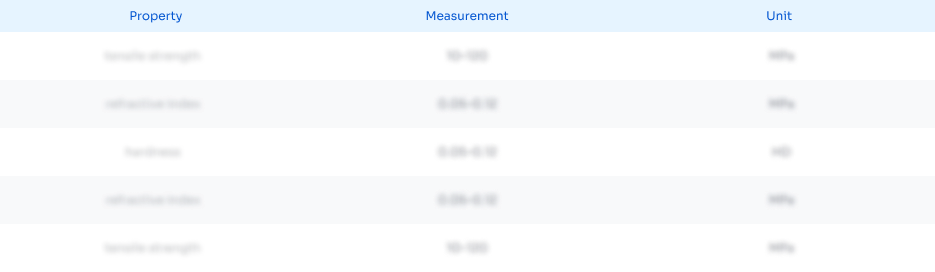
Abstract
Description
Claims
Application Information

- R&D
- Intellectual Property
- Life Sciences
- Materials
- Tech Scout
- Unparalleled Data Quality
- Higher Quality Content
- 60% Fewer Hallucinations
Browse by: Latest US Patents, China's latest patents, Technical Efficacy Thesaurus, Application Domain, Technology Topic, Popular Technical Reports.
© 2025 PatSnap. All rights reserved.Legal|Privacy policy|Modern Slavery Act Transparency Statement|Sitemap|About US| Contact US: help@patsnap.com