A method of preparing a C/gamma-Fe2O3 composite material from acid-regeneration desilication mud cakes
A technology for desiliconizing mud cakes and composite materials, applied in separation methods, chemical instruments and methods, alkali metal compounds, etc., can solve the problems of high iron citrine seed prices, large environmental pollution, and low economic efficiency, and achieve resource Recycling and reuse, less environmental pollution and strong continuity
- Summary
- Abstract
- Description
- Claims
- Application Information
AI Technical Summary
Problems solved by technology
Method used
Image
Examples
Embodiment 1
[0020] (a) Add water to the massive desiliconized mud cake, beat under heating at 80°C, add furfuryl alcohol of 5 times the mass of the desiliconized mud cake, and form a desiliconized mud slurry with good dispersibility.
[0021] (b) After the slurry in the above (a) is spray-dried at 110° C., a relatively fluffy furfuryl alcohol-coated desiliconized mud powder is obtained;
[0022] (c) Put the desiliconized mud powder obtained in the above (b) into the N with a heating rate of 2.5°C / min. 2 In a tube furnace with atmosphere protection at 800°C, after holding for 5 hours, C / γ-Fe can be obtained by cooling with the furnace 2 o 3 composite material.
Embodiment 2
[0024] (a) Add water to the massive desiliconized mud cake, beat under heating at 80°C, and add furfural of 4 times the mass of the desiliconized mud cake to form a desiliconized mud slurry with good dispersibility.
[0025] (b) After the slurry in the above (a) is spray-dried at 100° C., a relatively fluffy furfural-coated desiliconized mud powder is obtained;
[0026] (c) Put the desiliconized mud powder obtained in the above (b) into a tube furnace with a heating rate of 2°C / min under N2 atmosphere protection at 700°C, keep it warm for 6 hours, and then cool down with the furnace to obtain C / γ-Fe 2 o 3 composite material.
Embodiment 3
[0028] (a) Add water to the massive desiliconized mud cake, beat under heating at 80°C, and add 5 times the mass of desiliconized mud cake starch to form a desiliconized mud slurry with good dispersibility.
[0029] (b) Spray drying the slurry in (a) above at 100-120°C to obtain fluffy starch-coated desiliconized mud powder;
[0030] (c) Iron oxide Put the desiliconized mud powder obtained in the above (b) into a tube furnace with a heating rate of 2°C / min under N2 atmosphere protection at 600°C, keep it warm for 8 hours, and cool it with the furnace to obtain superfine C / γ-Fe 2 o 3 composite material.
PUM
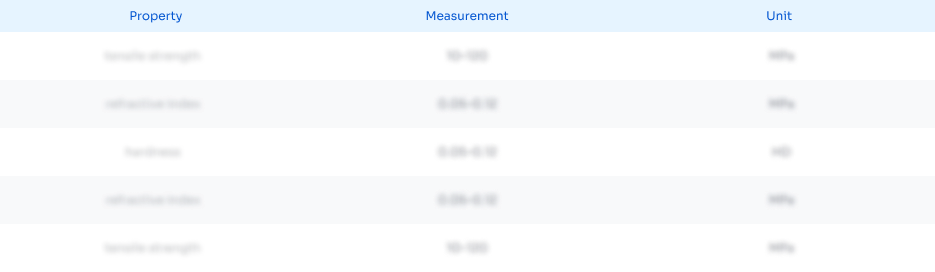
Abstract
Description
Claims
Application Information

- R&D Engineer
- R&D Manager
- IP Professional
- Industry Leading Data Capabilities
- Powerful AI technology
- Patent DNA Extraction
Browse by: Latest US Patents, China's latest patents, Technical Efficacy Thesaurus, Application Domain, Technology Topic, Popular Technical Reports.
© 2024 PatSnap. All rights reserved.Legal|Privacy policy|Modern Slavery Act Transparency Statement|Sitemap|About US| Contact US: help@patsnap.com