Special paper for surface of fan blade and preparation method for special paper
A special paper and fan surface technology, which is applied in the field of special paper for fan pages and its preparation, can solve the problems of single texture, single material, single fan page color, etc., achieve good protection, improve the surface strength of base paper, and the wind effect is stable and smooth Effect
- Summary
- Abstract
- Description
- Claims
- Application Information
AI Technical Summary
Problems solved by technology
Method used
Image
Examples
Embodiment 1
[0043] The preparation method of the special paper for the fan surface, the steps are as follows:
[0044] (1) Put the bleached coniferous pulp and bleached hardwood pulp into a pulper equipped with 45°C pulping water to fully disintegrate, and control the degree of knocking to 34°SR and 38°SR respectively, and after the mass concentration reaches 4.5%. Add the enhancer and stir well, then pump it into the slurry pool for standby;
[0045] (2) Dilute the filler with water to a mass concentration of 65%, add the pigment, then fully stir with a high-speed agitator at a speed of 3000 rpm to disperse the filler and pigment evenly, and finally pump it into the crushing tank of step (1) Mix evenly with the product obtained in step (1) to obtain a mixed slurry;
[0046](3) After the pulp mixed in step (2) is passed through a fiber disintegrating machine to disentangle the fibers, the fibers are cut and separated by a double disc mill beater; Fill the pool, add wet strength agent, d...
Embodiment 2
[0050] The preparation method of the special paper for the fan side of the fan, the steps are as follows:
[0051] (1) Put the bleached coniferous pulp and bleached hardwood pulp into a pulper equipped with 35°C pulping water to fully disintegrate, and control the degree of knocking to 31°SR and 35°SR respectively, and after the mass concentration reaches 4%. Add the enhancer and stir well, then pump it into the slurry pool for standby;
[0052] (2) Dilute the filler with water to a mass concentration of 55%, add the pigment, and then fully stir with a high-speed agitator at a speed of 3000 rpm to disperse the filler and pigment evenly, and finally pump it into the crushing tank of step (1) Mix evenly with the product obtained in step (1) to obtain a mixed slurry;
[0053] (3) After the pulp mixed in step (2) is passed through a fiber disintegrating machine to disentangle the fibers, the fibers are cut and separated by a double disc mill beater; Fill the pool, add wet streng...
Embodiment 3
[0057] The preparation method of the special paper for the fan side of the fan, the steps are as follows:
[0058] (1) Put the bleached coniferous pulp and bleached hardwood pulp into a pulper equipped with pulping water at 30°C to fully disintegrate, and control the degree of knocking to 34°SR and 38°SR respectively, and after the mass concentration reaches 4%. Add the enhancer and stir well, then pump it into the slurry pool for standby;
[0059] (2) Dilute the filler with water to a mass concentration of 65%, add the pigment, then fully stir with a high-speed agitator at a speed of 3000 rpm to disperse the filler and pigment evenly, and finally pump it into the crushing tank of step (1) Mix evenly with the product obtained in step (1) to obtain a mixed slurry;
[0060] (3) After the pulp mixed in step (2) is passed through a fiber disintegrating machine to disentangle the fibers, the fibers are cut and separated by a double disc mill beater; Fill the pool, add wet strengt...
PUM
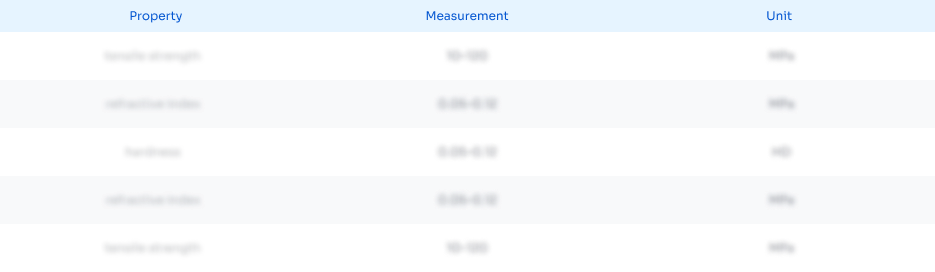
Abstract
Description
Claims
Application Information

- Generate Ideas
- Intellectual Property
- Life Sciences
- Materials
- Tech Scout
- Unparalleled Data Quality
- Higher Quality Content
- 60% Fewer Hallucinations
Browse by: Latest US Patents, China's latest patents, Technical Efficacy Thesaurus, Application Domain, Technology Topic, Popular Technical Reports.
© 2025 PatSnap. All rights reserved.Legal|Privacy policy|Modern Slavery Act Transparency Statement|Sitemap|About US| Contact US: help@patsnap.com