Method for preparing starch size capable of achieving room temperature sizing
A starch slurry and starch mixing technology, which is applied in the direction of fiber type, textile and papermaking, fiber processing, etc., can solve the problems of difficult post-processing, low reaction efficiency, increase production cost, etc., so as to avoid the loss of strength and elasticity. , The effect of low warp breakage rate and production cost reduction
- Summary
- Abstract
- Description
- Claims
- Application Information
AI Technical Summary
Problems solved by technology
Method used
Image
Examples
Embodiment 1
[0016] Embodiment 1 pulping method A
[0017] (1) Slurry preparation
[0018] ①Fabric type: C40 S ×40 S 133×10094 ∥
[0019] ② Slurry formula: cornstarch 112.5kg, pentaerythritol 1.5kg, pentaerythritol stearate 2.1kg, solid polyacrylate slurry 6kg, wax flake 1.5kg, water 700kg.
[0020] ③Mulching: Add 700kg of cold water into the mixing tank, start the agitator, add cornstarch, pentaerythritol, pentaerythritol stearate, solid polyacrylate slurry, and wax flakes in succession, stir for 15 minutes, then heat up to 95°C, Slurry for 60 minutes, after the pulping time is up, open the pulp valve and pour the cooked slurry into the supply barrel, and set aside for later use.
[0021] ④Sizing
GA308
speed
50m / min
Dip method
Double Dip Double Pressure
Mixing tank viscosity
8.4s
Stock tank temperature
35℃
Tank Viscosity
9.5s
[0023] ⑤ Sizing performance and fabric effect
[0...
Embodiment 2
[0035] Embodiment 2 pulping method B
[0036] (1) Slurry preparation
[0037] ①Fabric type: C40 S ×40 S 133×7292 ∥
[0038] ② Slurry formula: tapioca starch 120kg, pentaerythritol 0.6kg, pentaerythritol stearate 4.56kg, liquid polyacrylate slurry 4kg, emulsifying wax 1.5kg, water 700kg.
[0039] ③Mulching: Add 700kg of cold water into the mixing tank, start the agitator, add tapioca starch, pentaerythritol, pentaerythritol stearate, liquid polyacrylate slurry and emulsified wax in succession, stir for 15 minutes, then heat up to 95°C, Slurry for 60 minutes, after the pulping time is up, open the pulp valve and pour the cooked slurry into the supply barrel, and set aside for later use.
[0040] ④Sizing
[0041] Sizing machine model
G142C
speed
50m / min
Dip method
Double Dip Double Pressure
Mixing tank viscosity
8.1s
Stock tank temperature
35℃
Tank Viscosity
9.2s
[0042] ⑤ Sizing performance and fa...
Embodiment 3
[0054] Embodiment 3 pulping method C
[0055] (1) Slurry preparation
[0056] ①Fabric type: C60 S ×60 S 133×5894 ∥
[0057]②Slurry formula: wheat starch 110kg, pentaerythritol 3.85kg, pentaerythritol stearate 0.33kg, rubber powder 10kg, emulsified oil 1.5kg, water 710kg.
[0058] ③Mulching: Add 710kg of cold water into the mixing tank, start the agitator, add potato starch, pentaerythritol, pentaerythritol stearate, rubber powder and emulsified oil in succession, stir for 15 minutes, then heat up to 95°C, suffocate the slurry for 60 minutes, and suffocate When the pulping time is up, open the pulping valve and put the boiled pulp into the supply barrel, set aside for later use.
[0059] ④Sizing
[0060] Sizing machine model
GA308
speed
50m / min
Dip method
Double Dip Double Pressure
[0061] Mixing tank viscosity
8.5s
Stock tank temperature
35℃
Tank Viscosity
9.6s
[0062] ⑤ Sizing perfor...
PUM
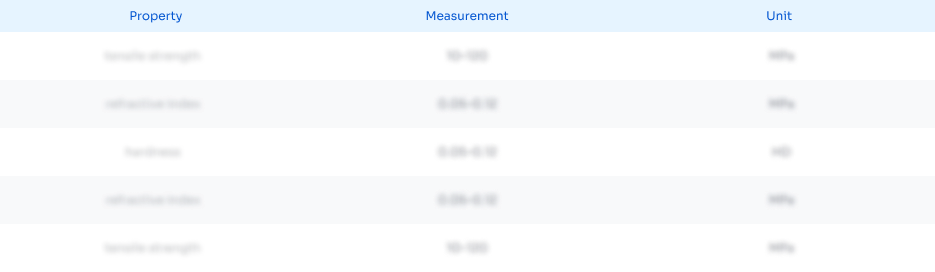
Abstract
Description
Claims
Application Information

- R&D Engineer
- R&D Manager
- IP Professional
- Industry Leading Data Capabilities
- Powerful AI technology
- Patent DNA Extraction
Browse by: Latest US Patents, China's latest patents, Technical Efficacy Thesaurus, Application Domain, Technology Topic, Popular Technical Reports.
© 2024 PatSnap. All rights reserved.Legal|Privacy policy|Modern Slavery Act Transparency Statement|Sitemap|About US| Contact US: help@patsnap.com