Method for preparing spinel-type complex oxide through co-precipitation, homogenization and spray drying
A composite oxide, spinel type technology, applied in ferrous oxides, chemical instruments and methods, zinc oxide/zinc hydroxide and other directions, can solve the problem of unsuitable large-scale industrial production, material loss product yield Low, uneven product components and other problems, to shorten the production cycle, simplify the production process, shorten the roasting time effect
- Summary
- Abstract
- Description
- Claims
- Application Information
AI Technical Summary
Problems solved by technology
Method used
Image
Examples
Embodiment
[0026] When preparing spinel-type composite oxides by co-precipitation-homogeneity-spray drying, the salt solution of metal A and metal B with a ratio of substance amount of 2:1 and alkaline solution are mixed at a certain precipitation temperature and pH value Co-precipitation reaction is carried out under , stirring speed and aging time, and the obtained material is washed with a certain temperature and an appropriate amount of deionized water, beaten and filtered several times. After the impurity content reaches the standard, the slurry is added to the homogenizer with a certain gap. Refining the slurry for a certain number of times, then spray-drying it under a suitable air inlet temperature and nozzle size, and finally roasting it under a suitable atmosphere and temperature for a period of time to obtain a spinel-type composite oxide.
[0027] The preparation process of Examples 1-17 of the present invention is the same as above, and the specific process conditions of the ...
PUM
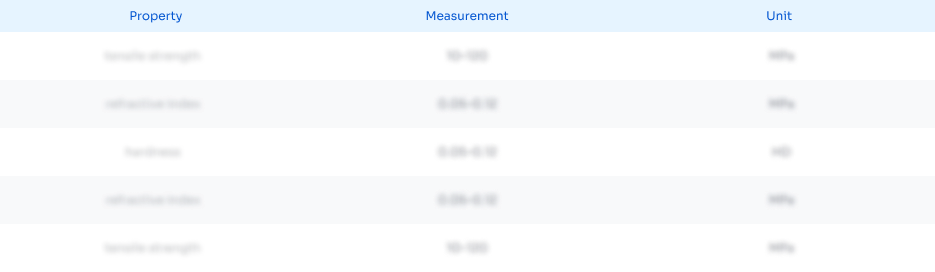
Abstract
Description
Claims
Application Information

- R&D
- Intellectual Property
- Life Sciences
- Materials
- Tech Scout
- Unparalleled Data Quality
- Higher Quality Content
- 60% Fewer Hallucinations
Browse by: Latest US Patents, China's latest patents, Technical Efficacy Thesaurus, Application Domain, Technology Topic, Popular Technical Reports.
© 2025 PatSnap. All rights reserved.Legal|Privacy policy|Modern Slavery Act Transparency Statement|Sitemap|About US| Contact US: help@patsnap.com