Large-shaft-shoulder stirring head suitable for high-speed friction-stir welding, and welding method
A technology of friction welding and high-speed stirring, which is applied in welding equipment, non-electric welding equipment, metal processing equipment, etc., can solve the problems that it is difficult to realize high-speed friction stir welding of medium and thick plates, and achieve improved welding efficiency, good weld shape, and reduced The effect of the probability of forming defects
- Summary
- Abstract
- Description
- Claims
- Application Information
AI Technical Summary
Problems solved by technology
Method used
Image
Examples
specific Embodiment approach 1
[0029] Specific implementation mode one: combine Figure 1 to Figure 5 Describe this embodiment, a large shoulder stirring head suitable for high-speed friction stir welding described in this embodiment, the large shoulder stirring head includes a clamping area 1-1, a shoulder 1-2 and a stirring needle 1-3 , the center of the clamping area 1-1, the center of the shaft shoulder 1-2 and the center of the stirring needle 1-3 are set coaxially; the shaft shoulder 1-2 is a large shaft shoulder with a diameter D1 greater than 5 times the thickness of the workpiece to be welded, and the shaft shoulder 1 The variable-groove deep Archimedean spiral groove that is different from the conventional equal-groove deep Archimedean spiral groove is processed on the -2 plane. The curve equation of the variable-groove deep Archimedean spiral groove is ρ=a+bθ, and ρ is Polar diameter, θ is the polar angle, indicating the total degree of the Archimedes spiral, a is the polar diameter when θ = 0, b...
specific Embodiment approach 2
[0030] Specific implementation mode two: combination figure 1 Illustrate the present embodiment, the curve equation of the processed Archimedes spiral groove on the shaft shoulder 1-2 plane in the present embodiment is: The depth at the beginning of the spiral groove is 0.5mm, and the depth at the end of the spiral groove is 1.0mm; the lead of the first set of taper threads on the side of the stirring needle 1-3 is 2mm, and the lead of the second set of taper threads is 12mm. Other compositions and connections are the same as in the first embodiment.
[0031] The technical effect of this embodiment is: the large shoulder stirring head can ensure sufficient heat input to form sufficient plastic metal in the high-speed friction stir welding process; the existence of the Archimedes spiral groove when the stirring head rotates counterclockwise The metal is guided from the end of the spiral groove along the spiral groove to the beginning of the spiral groove, and as the flow dist...
specific Embodiment approach 3
[0032] Specific implementation mode three: combination Figure 4 to Figure 5 Describe this embodiment, a kind of high-speed friction stir welding method described in this embodiment is characterized in that it comprises the following steps:
[0033] Step 1. Determination of the dimensions of the large shoulder stirring head:
[0034] Determine the diameter D1 of the shoulder 1-2, the root diameter D2 of the stirring needle 1-3, and the end diameter of the stirring needle 1-3 according to the thickness h of the first welded workpiece 2-1 and the second welded workpiece 2-2 D3 and the length L of the stirring needle 1-3; wherein the diameter D1 of the shoulder 1-2 is 5-10 times the thickness h of the first welded workpiece 2-1 and the second welded workpiece 2-2, and the stirring needle 1- The root diameter D2 of 3 is 2-4 times the thickness h of the first welded workpiece 2-1 and the second welded workpiece 2-2, and the end diameter D3 of the stirring pin 1-3 is the first welded...
PUM
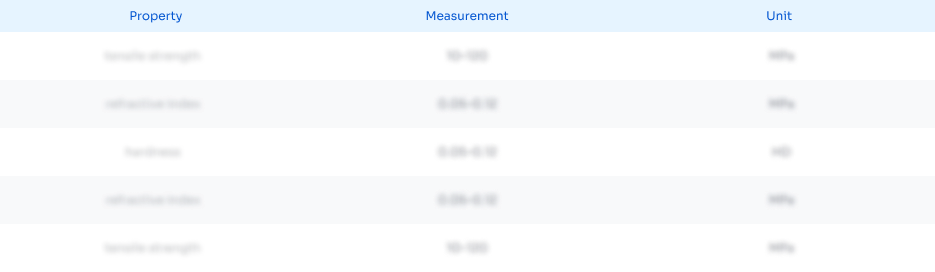
Abstract
Description
Claims
Application Information

- R&D Engineer
- R&D Manager
- IP Professional
- Industry Leading Data Capabilities
- Powerful AI technology
- Patent DNA Extraction
Browse by: Latest US Patents, China's latest patents, Technical Efficacy Thesaurus, Application Domain, Technology Topic, Popular Technical Reports.
© 2024 PatSnap. All rights reserved.Legal|Privacy policy|Modern Slavery Act Transparency Statement|Sitemap|About US| Contact US: help@patsnap.com