Microalloy strengthened hard pure gold and preparation method thereof
A hard and intermediate alloy technology, applied in the field of micro-alloy strengthening hard pure gold and its preparation, can solve problems such as difficulty in realization
- Summary
- Abstract
- Description
- Claims
- Application Information
AI Technical Summary
Problems solved by technology
Method used
Examples
preparation example Construction
[0024] In some aspects of the present invention, a method for preparing the aforementioned hard solid gold material is also proposed, including:
[0025] The 99.99% pure gold material is mixed with the strengthening element calcium and titanium mixed powder according to the mass ratio of 9:1, and the master alloy is prepared by vacuum induction melting;
[0026] Then, the prepared master alloy and 99.99% pure gold material are subjected to secondary vacuum induction melting at a weight ratio of 1:9. After the alloy is melted at high temperature, rare earth element powder is added, and casting or block making is carried out after refining.
[0027] Preferably, the mass ratio of the strengthening elements calcium and titanium added in the method is 1-4:5-8.
[0028] Preferably, the added amount of the rare earth element powder is 0.01-0.1% of the mass of the final smelted product. The rare earth element powder added in such a proportion is dysprosium and / or terbium element powd...
Embodiment 1
[0033] First of all, the master alloy is refined by batching, or called "filling mouth", the batching ratio is: calcium 1.4%, titanium 6.8% (in the form of mixed powder), and the rest is 99.99% pure gold material. Add the mixed material into the crucible of the vacuum melting furnace, and start vacuuming. Vacuum up to 3.7×10 -3 After Pa, start heating and smelting, and the melt temperature is measured by an infrared thermometer. When the temperature reaches 1480°C, reduce the current and start refining. The refining time is 30 seconds. After the melting is completed, pour it into a copper crucible to obtain an intermediate alloy. Then mix the master alloy and 99.99% pure gold material according to the ratio of 1:9, vacuum melting again, cover the upper layer with pure gold when adding materials, and after the alloy is completely melted through the observation window, quickly add the rare earth element Dysprosium powder, the amount added It is 0.05%, electromagnetically stirr...
Embodiment 2
[0036] Firstly, the master alloy is refined by batching, and the batching ratio is: calcium 2.5%, titanium 5.1% (in the form of mixed powder), and the rest is 99.99% pure gold material. Add the mixed material into the crucible of the vacuum melting furnace, and start vacuuming. Vacuum up to 3.4×10 -3 After Pa, start heating and smelting, and the melt temperature is measured by an infrared thermometer. When the temperature reaches 1510°C, reduce the current and start refining. The refining time is 35 seconds. After the melting is completed, pour into a copper crucible to obtain an intermediate alloy. Then mix the intermediate alloy and pure gold according to the ratio of 1:9, and carry out vacuum smelting again. When adding materials, cover the upper layer with pure gold. After the alloy is completely melted through the observation window, quickly add dysprosium powder, a rare earth element, in an amount of 0.06%. , electromagnetically stirred evenly, then refined for 28 seco...
PUM
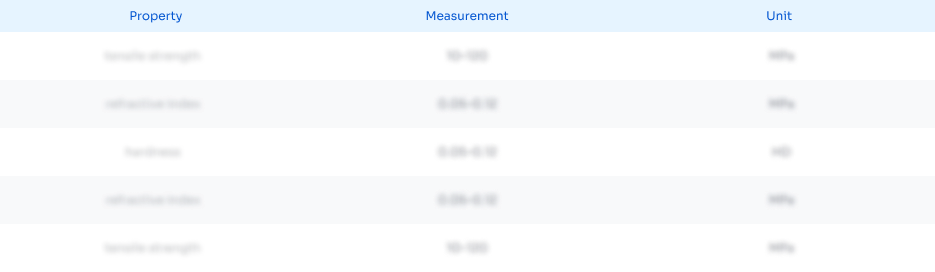
Abstract
Description
Claims
Application Information

- Generate Ideas
- Intellectual Property
- Life Sciences
- Materials
- Tech Scout
- Unparalleled Data Quality
- Higher Quality Content
- 60% Fewer Hallucinations
Browse by: Latest US Patents, China's latest patents, Technical Efficacy Thesaurus, Application Domain, Technology Topic, Popular Technical Reports.
© 2025 PatSnap. All rights reserved.Legal|Privacy policy|Modern Slavery Act Transparency Statement|Sitemap|About US| Contact US: help@patsnap.com