OLED display device and packaging technology thereof
A technology of display device and packaging process, which is applied in the field of OLED display device and its packaging process, can solve the problems of not achieving marginalization of the position, increasing the display area, and slow packaging speed, so as to achieve the maximum, realize the display area, improve the The effect of package speed
- Summary
- Abstract
- Description
- Claims
- Application Information
AI Technical Summary
Problems solved by technology
Method used
Image
Examples
Embodiment 1
[0027] Embodiment 1 provides a packaging process for OLED display devices, such as figure 1 shown, including the following steps:
[0028] Step 1: Cut the packaging glass cover plate and substrate to form multiple independent glass cover plate units and substrate units, and preheat the low-temperature glass frit to molten glass for use;
[0029] Step 2: Place the packaging glass cover on the substrate, the size of the packaging glass cover is smaller than the size of the substrate, and the distance between the outer edge of the substrate and the outer edge of the packaging glass cover is 0.5mm-2.0mm, optional 0.5-1.5 mm, more preferably 1 mm, and a circle of exposed peripheral parts of the substrate can be formed on the outer edge of the substrate.
[0030] Step 3: Coat the molten low-temperature glass water on the peripheral part of the exposed substrate with a robot or other equipment that can be used for coating work. There is a length difference between the package cover ...
Embodiment 2
[0031] Embodiment 2 provides a packaging process for OLED display devices, such as figure 2 shown, including the following steps:
[0032] Step 1: Cut the packaging glass cover plate and substrate to form multiple independent glass cover plate units and substrate units, and preheat the low-temperature glass frit to molten glass water for use. The melting temperature of the low-temperature glass frit is lower than that of the glass substrate, generally 320°C-600°C.
[0033] Step 2: Prefabricate a notch on the outer edge of the sealing glass cover plate. The notch is designed around the outer edge of the sealing glass cover plate. The shape of the notch can be arc-shaped or square. The notch is along the vertical direction and the The depth in the horizontal direction is 0.5mm-2mm, preferably 0.5mm-1.5mm. The vertical depth of the notch is less than or equal to the thickness of the package cover. The thickness of the packaging cover plate is 1.0mm-2.0mm.
[0034] Step 3: pl...
PUM
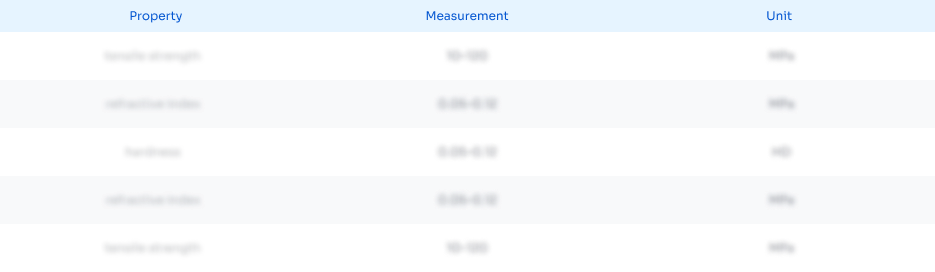
Abstract
Description
Claims
Application Information

- R&D
- Intellectual Property
- Life Sciences
- Materials
- Tech Scout
- Unparalleled Data Quality
- Higher Quality Content
- 60% Fewer Hallucinations
Browse by: Latest US Patents, China's latest patents, Technical Efficacy Thesaurus, Application Domain, Technology Topic, Popular Technical Reports.
© 2025 PatSnap. All rights reserved.Legal|Privacy policy|Modern Slavery Act Transparency Statement|Sitemap|About US| Contact US: help@patsnap.com