Pretreatment method for deep processing of coal tar
A technology for deep processing of coal tar, which is applied in the pretreatment of coal tar deep processing and the pretreatment of coal tar raw materials, and can solve the problems of low density, environmental pollution, and no desalination treatment facilities, etc.
- Summary
- Abstract
- Description
- Claims
- Application Information
AI Technical Summary
Problems solved by technology
Method used
Image
Examples
example 1
[0027] Centrifuge the coal tar and filter it twice to ensure that the particle size of mechanical impurities is not greater than 15 μm, heat the coal tar to 135° C., inject water accounting for 10% of the total weight of the coal tar, and add a demulsifier accounting for 50 μg / g of the total weight of the coal tar; The demetallization agent is 40 μg / g, mixed in a static mixer, the mixing intensity is 50KPa, the electric field strength in the electric stripping tank is 800V / cm, and it stays in the electric field for 40 minutes. The properties of tar after three-stage electric stripping and properties after hydrogenation are shown in the table below
[0028]
example 2
[0030] The coal tar is subjected to centrifugation and filtered twice, the particle size of mechanical impurities is not greater than 15 μm, the coal tar is heated to 130° C., and water accounting for 8% of the total weight of the coal tar is injected, and a demulsifier accounting for 60 μg / g of the total weight of the coal tar is added; The demetallization agent is 70 μg / g, mixed in a static mixer, the mixing intensity is 60KPa, the electric field strength in the electro-stripping tank is 100V / cm, and it stays in the electric field for 35 minutes. The properties of the tar after three-stage electro-stripping and the properties after hydrogenation are shown in the table below
[0031]
PUM
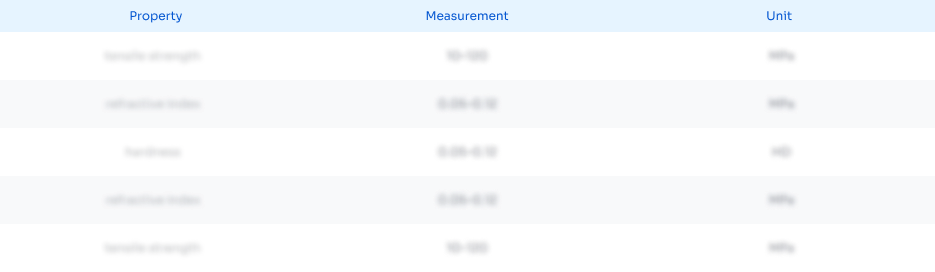
Abstract
Description
Claims
Application Information

- R&D
- Intellectual Property
- Life Sciences
- Materials
- Tech Scout
- Unparalleled Data Quality
- Higher Quality Content
- 60% Fewer Hallucinations
Browse by: Latest US Patents, China's latest patents, Technical Efficacy Thesaurus, Application Domain, Technology Topic, Popular Technical Reports.
© 2025 PatSnap. All rights reserved.Legal|Privacy policy|Modern Slavery Act Transparency Statement|Sitemap|About US| Contact US: help@patsnap.com