Highly polished pre-hardening plastic die steel and manufacturing process thereof
A technology of plastic mold and manufacturing process, applied in the field of high-polishing pre-hardened plastic mold steel and its manufacturing process, can solve the problems of increasing the manufacturing cost and high price of automobile products, and achieve the improvement of manufacturing level and market competitiveness, low alloy cost, The effect of high polishing performance
- Summary
- Abstract
- Description
- Claims
- Application Information
AI Technical Summary
Problems solved by technology
Method used
Image
Examples
Embodiment 1
[0041] A highly polished pre-hardened plastic mold steel matrix is composed of the following components in mass percentage: C0.20%; Si0.10%; Mn0.80%; Cr0.80%; W0.60%; Mo0.50%; V0.07%; P0.015%; S0.002%; B0.003%;
[0042] Ni1.00%; Nb0.06%; the rest is Fe.
[0043] A manufacturing process of highly polished pre-hardened plastic mold steel has the following steps:
[0044] Step A. electric furnace smelting: smelting in an electric arc furnace according to the composition of the above components, then refining outside the furnace and vacuum degassing, casting into steel ingots and sending them to the forging heating furnace;
[0045] Step B. High-temperature diffusion heat treatment: heat the steel ingot treated in step A at high temperature, keep the temperature at 1150-1250°C, and keep it warm for 15-20 hours;
[0046] Step C. Forging hot processing: cooling the steel ingot treated in step B to a temperature range of 900~1200°C for multi-directional forging processing, adopti...
Embodiment 2
[0052] A highly polished pre-hardened plastic mold steel matrix is composed of the following components in mass percentage: C0.20%; Si0.20%; Mn1.00%; Cr0.70%; W0.50%; Mo0.70%; V0.06%; P0.010%; S0.002%; B0.005%; Ni0.80%; Nb0.06%; the rest is Fe.
[0053] A manufacturing process of highly polished pre-hardened plastic mold steel has the following steps:
[0054] Step A. electric furnace smelting: smelting in an electric arc furnace according to the composition of the above components, then refining outside the furnace and vacuum degassing, casting into steel ingots and sending them to the forging heating furnace;
[0055] Step B. High-temperature diffusion heat treatment: heat the steel ingot treated in step A at high temperature, keep the temperature at 1150-1250°C, and keep it warm for 15-20 hours;
[0056] Step C. Forging hot processing: cooling the steel ingot treated in step B to a temperature range of 900~1200°C for multi-directional forging processing, adopting two ups...
Embodiment 3
[0062] A highly polished pre-hardened plastic mold steel matrix is composed of the following components in mass percentage: C0.18%; Si0.18%; Mn1.00%; Cr1.00%; W0.80%; Mo0.50%; V0.05%; P0.020%; S0.003%; B0.004%; Ni1.00%; Nb0.10%; the rest is Fe.
[0063] A manufacturing process of highly polished pre-hardened plastic mold steel has the following steps:
[0064] Step A. electric furnace smelting: smelting in an electric arc furnace according to the composition of the above components, then refining outside the furnace and vacuum degassing, casting into steel ingots and sending them to the forging heating furnace;
[0065] Step B. High-temperature diffusion heat treatment: heat the steel ingot treated in step A at high temperature, keep the temperature at 1150-1250°C, and keep it warm for 15-20 hours;
[0066] Step C. Forging hot processing: cooling the steel ingot treated in step B to a temperature range of 900~1200°C for multi-directional forging processing, adopting two ups...
PUM
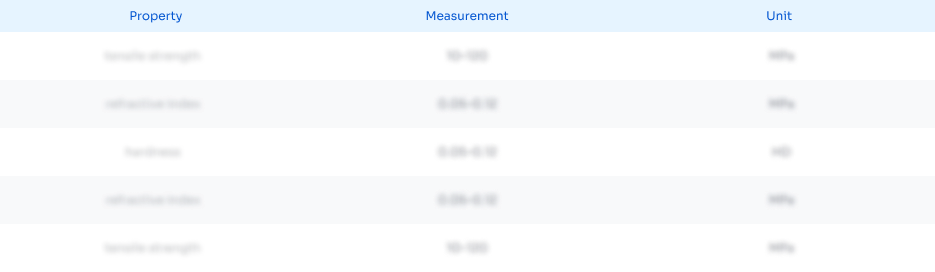
Abstract
Description
Claims
Application Information

- Generate Ideas
- Intellectual Property
- Life Sciences
- Materials
- Tech Scout
- Unparalleled Data Quality
- Higher Quality Content
- 60% Fewer Hallucinations
Browse by: Latest US Patents, China's latest patents, Technical Efficacy Thesaurus, Application Domain, Technology Topic, Popular Technical Reports.
© 2025 PatSnap. All rights reserved.Legal|Privacy policy|Modern Slavery Act Transparency Statement|Sitemap|About US| Contact US: help@patsnap.com