Biodegradable material and preparation method and use thereof
A biodegradable material and degradable film technology, applied in the field of polymer materials, can solve the problems of thermoplasticity, poor melt strength and ductility, and achieve the effects of good flexibility, good flexibility, and scientific ingredients.
- Summary
- Abstract
- Description
- Claims
- Application Information
AI Technical Summary
Problems solved by technology
Method used
Image
Examples
Embodiment 1
[0031] The biodegradable material described in this embodiment is made of the following components: polylactic acid 10kg, PBAT 55kg, talcum powder 35kg, acetyl tributyl citrate 3kg, 2,2-methylenebis(4-methyl-6-tert Butylphenol) 0.3kg, carbodiamine 0.5kg, polymeric epoxy functional group compound, ethylene bis stearic acid amide 0.8kg, vinyl acetate polyester compound 0.8kg, polyethylene glycol resin grafted GMA copolymer 0.7kg, stearic acid 0.5kg, ethylene bis stearic acid amide 0.5kg, epoxy soybean oil 0.3kg.
[0032] Add the talc powder into the high-speed mixer for mixing, the running time is 10-20 minutes, the speed of the high-speed mixer is 280-320 rpm, and the temperature inside the machine is 95-120°C; (Note: it is also possible not to dry) the talc After the powder is dried, put it into the cooling mixer. The speed of the cooling mixer is 300-600 rpm to cool the material below 40°C, and add polylactic acid, PBAT and various additives, and add it to a high-speed mixer ...
Embodiment 2
[0035] The biodegradable material described in this embodiment is made of the following components: 35kg of polylactic acid, 55kg of PBAT, 10kg of talcum powder, 0.8kg of vinyl acetate polyester compound, 0.7kg of polyethylene glycol grafted AGM copolymer, polyhydrazide Imine graft reactive epoxy functional compound 0.8kg, tributyl citrate 1.5kg, 2,2-methylenebis(4-methyl-6-tert-butylphenol) 0.3kg, carbodiamine 0.5kg, 0.5kg of ethylene bis stearic acid amide, 0.5kg of stearic acid, 0.3kg of epoxy soybean oil.
[0036] Add the talc powder into the high-speed mixer for mixing, the running time is 10-20 minutes, the speed of the high-speed mixer is 280-320 rpm, and the temperature inside the machine is 95-120°C; (Note: it is also possible not to dry) the talc After the powder is dried, put it into the cooling mixer. The speed of the cooling mixer is 300-600 rpm to cool the material below 40°C, and add polylactic acid, PBAT and various additives, and add it to a high-speed mixer f...
Embodiment 3
[0039]The biodegradable material described in this embodiment is prepared from the following components by weight: polylactic acid 5kg, calcium carbonate 40kg, PBAT 10kg, and auxiliary agent 12.6kg; the auxiliary agent includes: polyethylene glycol ester grafted GMA Copolymer 2.2kg, tributyl citrate 2.5kg, tripentyl citrate 2.5kg, polymeric epoxy functional group compound (polyhydrazide imine graft reactive epoxy functional group compound) 1.5kg, 2,2- Methylenebis(4-methyl-6-tert-butylphenol) 0.5kg, vinyl acetate polyester compound 2.0kg, carbodiamine 0.4kg, isocyanate 0.2kg, stearic acid 0.3kg, oleic acid 0.5kg .
[0040] Add calcium carbonate into the high-speed mixer for mixing, the running time is 10-20 minutes, the speed of the high-speed mixer is 280-320 rpm, and the temperature inside the machine is 95-120°C; After the powder is dried, put it into the cooling mixer. The speed of the cooling mixer is 300-600 rpm to cool the material below 40°C, and add polylactic acid, ...
PUM
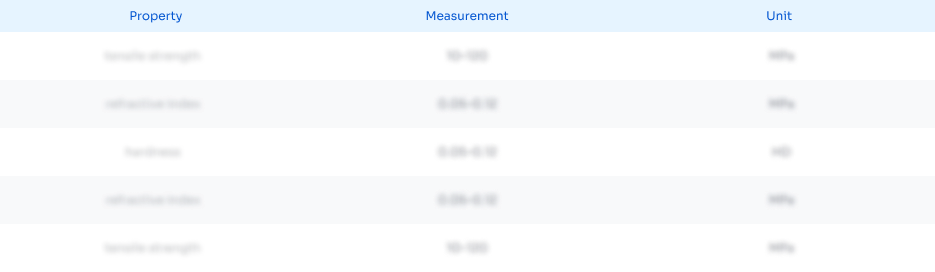
Abstract
Description
Claims
Application Information

- R&D
- Intellectual Property
- Life Sciences
- Materials
- Tech Scout
- Unparalleled Data Quality
- Higher Quality Content
- 60% Fewer Hallucinations
Browse by: Latest US Patents, China's latest patents, Technical Efficacy Thesaurus, Application Domain, Technology Topic, Popular Technical Reports.
© 2025 PatSnap. All rights reserved.Legal|Privacy policy|Modern Slavery Act Transparency Statement|Sitemap|About US| Contact US: help@patsnap.com