Preparation method of continuous oxide fiber reinforced oxide ceramic based composite
A technology for oxide ceramics and composite materials, which is applied in the field of preparation of continuous oxide fiber reinforced oxide ceramic matrix composite materials, can solve the problems of low content of sol ceramics, inability to perform, and difficult to store, and avoid the decrease of fiber strength or Powdering, flexible structural design, avoiding the effect of density gradients
- Summary
- Abstract
- Description
- Claims
- Application Information
AI Technical Summary
Problems solved by technology
Method used
Examples
preparation example Construction
[0022] (1) Preparation of slurry
[0023] Put the oxide ceramic powder, the oxide ceramic organic precursor solution, and the organic solvent in a ball mill pot and mix them uniformly by weight, wherein the oxide ceramic powder is 40wt% to 80wt%, and the organic oxide ceramic precursor 10wt% to 50wt%, the organic solvent is 10wt% to 40wt%, and the organic slurry with evenly dispersed oxide ceramic powder is obtained;
[0024] (2) Preparation of continuous oxide fiber prepreg
[0025] Weave the continuous oxide fiber into a two-dimensional fabric, and then pre-cut the above-mentioned oxide fiber fabric of a certain size according to the component size requirements, and evenly paint the organic slurry prepared in step (1) on the oxide fiber fabric surface, and place the fiber fabric coated with the slurry in a vacuum oven for solvent removal treatment, and obtain the prepreg after the slurry on the surface of the fiber fabric is dried;
[0026] (3) Preparation of low porosity ...
Embodiment 1
[0031] Put 60wt% of alumina powder, 20wt% of polyaluminoxane solution, and 20wt% of toluene solution in a certain proportion into a ball mill jar and mix them evenly to prepare alumina ceramic slurry. Apply the above organic slurry evenly on the surface of the pre-cut alumina fiber plain weave fabric produced by Mitsubishi Corporation of Japan, and place the fiber fabric coated with the slurry in a vacuum oven for solvent removal treatment, and wait for the surface slurry of the fiber fabric to dry Then the prepreg is obtained. The fiber volume fraction is controlled at 40%.
[0032] The above prepregs are placed in a metal mold to be stacked, and molded in a vacuum press, and then the molded preform is heat treated in a cracking furnace. The heat treatment temperature is 1150 ° C, and the heat treatment time is 2 hours. Finally, Low porosity ceramic matrix composite preform. Then the polyaluminoxane solution is used to carry out repeated impregnation-cracking process on the...
Embodiment 2
[0034] Put 50wt% of mullite powder, 15wt% of polyaluminoxane solution, 15wt% of vinyl silane solution, and 20wt% of chloroform solution into a ball mill tank according to a certain proportion and mix them uniformly to prepare mullite ceramic slurry . Apply the above organic slurry evenly on the surface of the pre-cut mullite fiber twill fabric produced by 3M Company in the United States, and place the fiber fabric coated with the slurry in a vacuum oven for solvent removal treatment. After drying, a prepreg is obtained. The fiber volume fraction is controlled at 42%.
[0035]The above prepregs are placed in a metal mold to be laminated, and molded in a vacuum press, and then the molded preform is heat treated in a cracking furnace. The heat treatment temperature is 1100 ° C, and the heat treatment time is 3 hours. Finally, Low porosity ceramic matrix composite preform. The polyaluminoxane solution and vinyl silane solution are mixed in proportion, and the preform is subject...
PUM
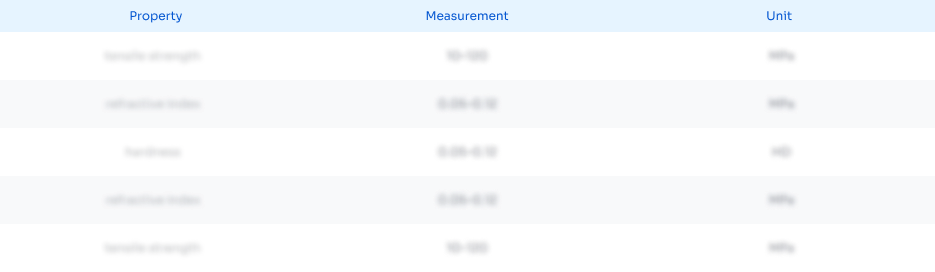
Abstract
Description
Claims
Application Information

- Generate Ideas
- Intellectual Property
- Life Sciences
- Materials
- Tech Scout
- Unparalleled Data Quality
- Higher Quality Content
- 60% Fewer Hallucinations
Browse by: Latest US Patents, China's latest patents, Technical Efficacy Thesaurus, Application Domain, Technology Topic, Popular Technical Reports.
© 2025 PatSnap. All rights reserved.Legal|Privacy policy|Modern Slavery Act Transparency Statement|Sitemap|About US| Contact US: help@patsnap.com