Steel grain refining heat treatment method for heavy-load locomotive gear
A heat treatment method and technology for heavy-duty locomotives, applied in the field of heat treatment, can solve the problems of reducing the strength and toughness of gears, high carburizing temperature of gears, coarse grains, etc., and achieve the effect of improving comprehensive mechanical properties and improving wear resistance
- Summary
- Abstract
- Description
- Claims
- Application Information
AI Technical Summary
Problems solved by technology
Method used
Image
Examples
Embodiment Construction
[0032] Objects, advantages and features of the present invention will be illustrated and explained by the following non-limiting description of preferred embodiments. These embodiments are only typical examples of applying the technical solutions of the present invention, and all technical solutions formed by adopting equivalent replacements or equivalent transformations fall within the protection scope of the present invention.
[0033] The present invention discloses a grain refinement heat treatment method for steel for heavy-duty locomotive gears. Firstly, the tendency of austenite grain growth is suppressed by lowering the temperature in the carburizing process, and then through isothermal normalizing, high-return quenching and secondary Quenching is used to gradually refine the grains of the core and surface layers of the steel for heavy-duty locomotive gears to form a fine acicular martensite structure, thereby improving the comprehensive mechanical properties of the ste...
PUM
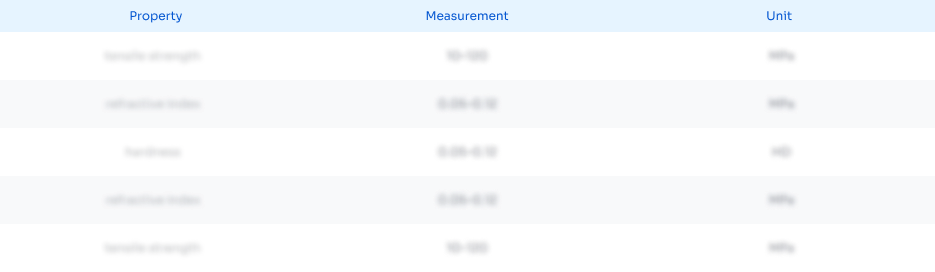
Abstract
Description
Claims
Application Information

- R&D
- Intellectual Property
- Life Sciences
- Materials
- Tech Scout
- Unparalleled Data Quality
- Higher Quality Content
- 60% Fewer Hallucinations
Browse by: Latest US Patents, China's latest patents, Technical Efficacy Thesaurus, Application Domain, Technology Topic, Popular Technical Reports.
© 2025 PatSnap. All rights reserved.Legal|Privacy policy|Modern Slavery Act Transparency Statement|Sitemap|About US| Contact US: help@patsnap.com