Halogen-free flame-retardant heat-resistant weather-resistant polypropylene nano composite insulating material for automobile wire and preparation method thereof
A weather-resistant polypropylene and insulating material technology, applied in the direction of insulated conductors, insulated cables, organic insulators, etc., can solve the problems of deteriorating material processing and mechanical properties, unqualified long-term insulation performance, and inability to adjust the color of insulating materials. Good properties and dispersive peeling properties, promoting synergistic flame retardant effect, and the effect of environmental stress cracking resistance
- Summary
- Abstract
- Description
- Claims
- Application Information
AI Technical Summary
Problems solved by technology
Method used
Image
Examples
Embodiment 1
[0040] (1) Preparation of polypropylene nanocomposite: 100 parts of base resin polypropylene, 10 parts of compatibilizing resin, 4.0 parts of nano-inorganic compound, 0.5 part of composite antioxidant, 0.4 part of metal deactivator, 1.0 part of ultraviolet absorber, 1.0 part of the compound lubricant A was put into a high-speed mixer, stirred for 3 minutes at room temperature at a rotation speed of 430-475 rpm, and discharged, and then extruded and pelletized by a twin-screw extruder with reverse thread section. The length-to-diameter ratio of the twin-screw extruder is L / D=44, and the extrusion temperature is 110-140℃ in the feeding section, 150-190℃ in the compression section, and 180-175℃ in the homogenization section. Among them: the base resin is a propylene-ethylene block copolymer with an ethylene molar content of 10%, and MFR=2.2g / (10min, 2.16kg); the compatibilizing resin is a graft of polypropylene maleic anhydride monomer, grafted The branch monomer content is 1.0wt%...
Embodiment 2
[0044] This embodiment provides a halogen-free flame-retardant, heat-resistant and weather-resistant polypropylene nano-composite insulating material for automotive wires. The weight composition is as follows: 45 parts of polypropylene nano-composite and 55 parts of halogen-free flame-retardant masterbatch. Among them, the composition weight ratio of the polypropylene nanocomposite is: 100 parts of base resin polypropylene, 12 parts of compatibilizing resin, 6.0 parts of nano-inorganic compounds, 0.6 parts of composite antioxidant, 0.6 parts of metal deactivator, and 1.5 parts of ultraviolet absorber. Parts, 1.5 parts of composite lubricant A; base resin is propylene-ethylene block copolymer with 10% ethylene mole content, MFR=2.2g / (10min, 2.16kg); compatibilizing resin is polypropylene Malay Acid anhydride monomer graft, the graft monomer content is 1.2wt%; the nano-inorganic compound is an organically modified montmorillonite containing modifier dihydrogenated tallow dimethyl ...
Embodiment 3
[0047] This embodiment provides a halogen-free flame-retardant, heat-resistant and weather-resistant polypropylene nano-composite insulating material for automotive wires. The weight composition is as follows: 50 parts of polypropylene nano-composite and 50 parts of halogen-free flame-retardant masterbatch. The composition weight ratio of polypropylene nanocomposite is: 100 parts of base resin polypropylene, 15 parts of compatibilizing resin, 8.0 parts of nano-inorganic compound, 1.0 part of composite antioxidant, 0.8 part of metal deactivator, and 2.0 part of ultraviolet absorber. Parts, composite lubricant A2.0 parts; base resin is propylene-ethylene block copolymer with 10% ethylene mole content, MFR=2.2g / (10min, 2.16kg); compatibilizing resin is polypropylene Malay The acid anhydride monomer graft, the graft monomer content is 1.5wt%; the nano-inorganic compound is an organically modified montmorillonite containing the modifier dihydrogenated tallow dimethyl ammonium and sil...
PUM
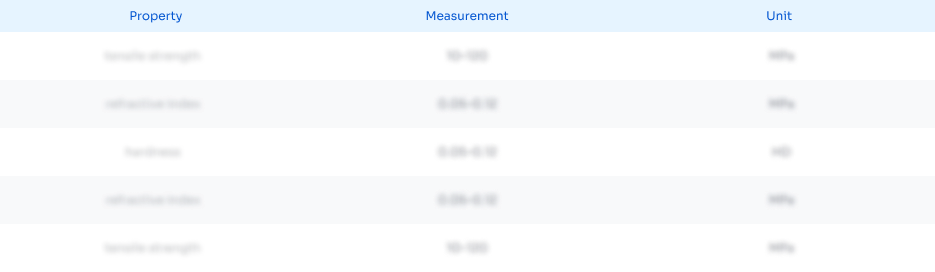
Abstract
Description
Claims
Application Information

- R&D
- Intellectual Property
- Life Sciences
- Materials
- Tech Scout
- Unparalleled Data Quality
- Higher Quality Content
- 60% Fewer Hallucinations
Browse by: Latest US Patents, China's latest patents, Technical Efficacy Thesaurus, Application Domain, Technology Topic, Popular Technical Reports.
© 2025 PatSnap. All rights reserved.Legal|Privacy policy|Modern Slavery Act Transparency Statement|Sitemap|About US| Contact US: help@patsnap.com