Composition of anti-fingerprint layer formed by multiple thin films and its preparation method
An anti-fingerprint layer and composition technology, applied in chemical instruments and methods, other chemical processes, paints containing biocide, etc., can solve problems such as high failure rate, high investment cost, poor performance, etc., to improve productivity , Save time and cost, reduce the effect of sticky time
- Summary
- Abstract
- Description
- Claims
- Application Information
AI Technical Summary
Problems solved by technology
Method used
Image
Examples
Embodiment 1
[0077] 90% by weight of SiO mixed with powder 2 , 6 weight percent Al 2 o 3 , 2 weight percent ZrO 2 , 2 weight percent TiO 2 Afterwards, polyvinyl alcohol (PVA), polyethylene glycol (PEG) and oleic acid were mixed as a binder in a ratio of 5:2:3, and then 1.2% by weight of the total powder was added and spray-dried. at 600kg / cm 2 After stamping the spray-dried powder under high pressure, it was sintered at 1150°C for 6 hours.
[0078] After placing the tempered glass in a chamber that can perform vacuum decompression, place the sintered substrate at the place where electron beam evaporation is performed, and place the anti-fingerprint chemical at the place where resistance heating evaporation is performed, and then use a vacuum pump to vacuum Decompress until 1.8×10 -4 Torr, and then use argon to etch the substrate. After the substrate has been etched, adjust the chamber to 1.5 x 10 -4 Torr, 80° C., and vapor deposition of the substrate was carried out by using an ele...
Embodiment 2
[0081] 90% by weight of SiO mixed with powder 2 , 8 weight percent Al 2 o 3 , 2 weight percent ZrO 2 Afterwards, polyvinyl alcohol, polyethylene glycol, and oleic acid were mixed in a ratio of 5:2:3 as a binder, and then spray-dried by adding 1.5% by weight of the total powder. at 600kg / cm 2 After stamping the spray-dried powder under high pressure, it was sintered at 1150°C for 6 hours.
[0082] at 550kg / cm 2 After stamping the spray-dried powder under high pressure, it was sintered at 1200°C for 8 hours.
[0083] After the tempered glass is placed in a chamber capable of vacuum decompression, the sintered substrate is placed in the place where the electron beam evaporation is performed, and the anti-fingerprint chemical is placed in the place where the resistance heating evaporation is performed, and then the vacuum is performed using a vacuum pump. Decompress until 1.8×10 -4 Torr, and then use argon to etch the substrate. After the substrate has been etched, adjust ...
Embodiment 3
[0086] 90% by weight of SiO mixed with powder 2 , 6 weight percent Al 2 o 3 , 4 weight percent TiO 2 Afterwards, polyvinyl alcohol, polyethylene glycol, and oleic acid were mixed in a ratio of 5:2:3 as a binder, and then spray-dried by adding 1.5% by weight of the total powder. at 550kg / cm 2 After stamping the spray-dried powder under high pressure, it was sintered at 1100°C for 10 hours.
[0087] After the tempered glass is placed in a chamber capable of vacuum decompression, the sintered substrate is placed in the place where the electron beam evaporation is performed, and the anti-fingerprint chemical is placed in the place where the resistance heating evaporation is performed, and then the vacuum is performed using a vacuum pump. Decompress until 1.8×10 -4 Torr, and then use argon to etch the substrate. After the substrate has been etched, adjust the chamber to 1.5 x 10 -4 Torr, 80° C., and vapor deposition of the substrate was carried out by using an electron beam ...
PUM
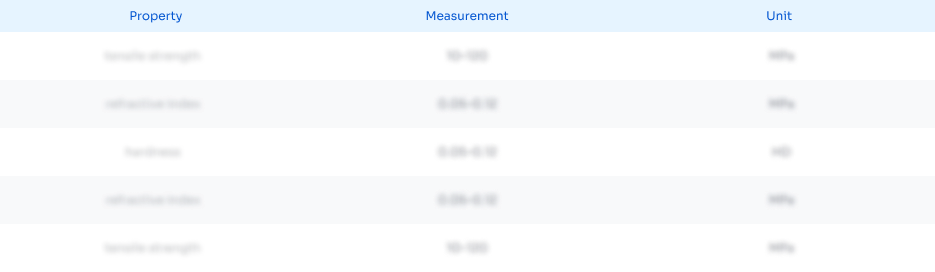
Abstract
Description
Claims
Application Information

- R&D
- Intellectual Property
- Life Sciences
- Materials
- Tech Scout
- Unparalleled Data Quality
- Higher Quality Content
- 60% Fewer Hallucinations
Browse by: Latest US Patents, China's latest patents, Technical Efficacy Thesaurus, Application Domain, Technology Topic, Popular Technical Reports.
© 2025 PatSnap. All rights reserved.Legal|Privacy policy|Modern Slavery Act Transparency Statement|Sitemap|About US| Contact US: help@patsnap.com