Method of metamorphosing hypo eutectic aluminum-silicon alloy by using rear earth Er
An aluminum-silicon alloy and hypoeutectic technology, which is applied in the field of aluminum alloy casting, can solve the problems of easy decay failure, easy generation of pores, and serious gas absorption tendency, etc., achieve shape and size optimization, overcome easy hydrogen evolution, and overcome easy decay Effect
- Summary
- Abstract
- Description
- Claims
- Application Information
AI Technical Summary
Problems solved by technology
Method used
Image
Examples
Embodiment 1
[0025] 1) In the process of batching hypoeutectic aluminum-silicon alloy, after preparing aluminum-silicon alloy, aluminum-copper alloy, aluminum-manganese alloy and pure magnesium, the mass ratio of Si element in the alloy is 7wt.%, Cu element in the alloy The mass ratio is 0.05wt.%, the mass ratio of Mn element in the alloy is 0.08wt.%, and the mass ratio of Mg element in the alloy is 0.35wt.%. 2) After melting pure aluminum and all alloys in a resistance furnace, heating to 720°C; 3) use a refining agent composed of hexachloroethane and sodium fluorosilicate (mass ratio 1:1) for refining and slag removal; 4) at 720°C, add aluminum-magnesium alloy wrapped in aluminum foil into the solution , and keep warm for 5 minutes after stirring; 5) add Er element to the alloy in a certain form, fully stir, Er element is controlled at 0.05-0.5wt.% in the alloy quality, preferably 0.3wt.%; 7) After adding Er element, carry out Insulation treatment, pouring into a metal mold preheated at ...
Embodiment 2
[0027] The difference from Example 1 is that the mass ratio of Si element in the alloy is 3wt.%, the mass ratio of Cu element in the alloy is 0.05wt.%, the mass ratio of Mn element in the alloy is 0.1wt.%, and the Mg element is in The mass ratio in the alloy is 0.3wt.%. After adding the Er element, heat preservation treatment between 680-740°C, preferably 720°C, and pour into a metal mold preheated at 250°C after heat preservation treatment. Under this condition, the same modification effect as in Example 1 can be achieved.
Embodiment 3
[0029] The difference from Example 1 is that the mass ratio of Si element in the alloy is 5wt.%, the mass ratio of Cu element in the alloy is 0.1wt.%, and the mass ratio of Mn element in the alloy is 0.1wt.%. Adding Er element Finally, keep it at 720°C for 10-60 minutes, preferably 10 minutes, and pour it into a metal mold preheated at 250°C after heat preservation treatment. Under this condition, the same modification effect as in Example 1 can be achieved.
PUM
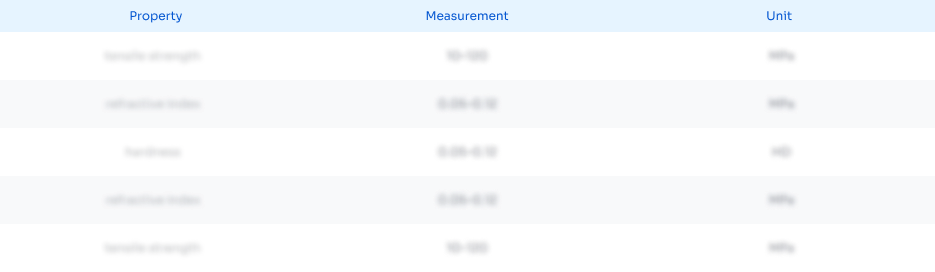
Abstract
Description
Claims
Application Information

- Generate Ideas
- Intellectual Property
- Life Sciences
- Materials
- Tech Scout
- Unparalleled Data Quality
- Higher Quality Content
- 60% Fewer Hallucinations
Browse by: Latest US Patents, China's latest patents, Technical Efficacy Thesaurus, Application Domain, Technology Topic, Popular Technical Reports.
© 2025 PatSnap. All rights reserved.Legal|Privacy policy|Modern Slavery Act Transparency Statement|Sitemap|About US| Contact US: help@patsnap.com