Stamping computer simulation calculating method with consideration of mold deformation
A technology of computer simulation and calculation method, applied in the direction of calculation, special data processing applications, instruments, etc., can solve the problem of low accuracy of high-strength steel stamping CAE, and achieve the effect of improving the accuracy of simulation calculation
- Summary
- Abstract
- Description
- Claims
- Application Information
AI Technical Summary
Problems solved by technology
Method used
Image
Examples
Embodiment Construction
[0029] Further description will be made below in conjunction with examples and accompanying drawings.
[0030] like figure 1 As shown, a stamping computer simulation calculation method considering the deformation of the mold includes the following steps:
[0031] Step 1: Build the mold model:
[0032] Simplify the mold structure based on the force of the mold, and use the actual drawing gap value generated by the deformation of the mold to offset the drawing surface, use the offset surface to cut the upper mold, and establish a mold model with the actual gap between the convex and concave molds;
[0033] Step 2: meshing the mold model constructed in step 1;
[0034] Perform finite element three-dimensional mesh division on the mold model, and import the divided mold into the finite element software Dynaform;
[0035] Among them, the grid size range is 2-10mm;
[0036] Step 3: In the finite element software Dynaform, mesh the sheet metal of the mold. The sheet metal element...
PUM
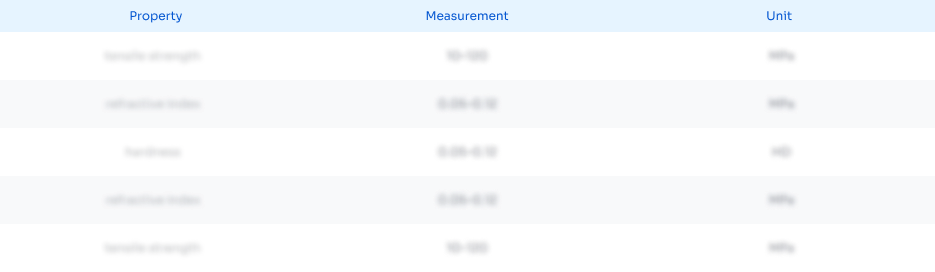
Abstract
Description
Claims
Application Information

- Generate Ideas
- Intellectual Property
- Life Sciences
- Materials
- Tech Scout
- Unparalleled Data Quality
- Higher Quality Content
- 60% Fewer Hallucinations
Browse by: Latest US Patents, China's latest patents, Technical Efficacy Thesaurus, Application Domain, Technology Topic, Popular Technical Reports.
© 2025 PatSnap. All rights reserved.Legal|Privacy policy|Modern Slavery Act Transparency Statement|Sitemap|About US| Contact US: help@patsnap.com