Preparation method for marine anticorrosive paint
A marine anti-corrosion and coating technology, which is applied in the direction of anti-corrosion coatings, epoxy resin coatings, coatings, etc., can solve problems such as not being fully considered and classified according to different usage occasions, and achieve excellent seawater corrosion resistance.
- Summary
- Abstract
- Description
- Claims
- Application Information
AI Technical Summary
Problems solved by technology
Method used
Image
Examples
Embodiment 1
[0020] A preparation method for marine anticorrosion paint, comprising the following steps:
[0021] Step 1, in parts by weight, take 2 parts of polyvinyl chloride, 1 part of xylene formaldehyde resin, 3 parts of zinc citrate, and 2 parts of epoxy resin, add them to 10 parts of solvent, and stir to obtain mixture A;
[0022] Step 2, in parts by weight, add 0.8 parts of neoprene rubber, 1 part of lecithin, 3 parts of sodium formaldehyde sulfoxylate, and 1 part of chlorinated paraffin to the mixture A obtained in step 1, and stir to obtain mixture B;
[0023] Step 3, in parts by weight, add 3 parts of rutile titanium dioxide, 2 parts of dispersant, 1 part of precipitated barium sulfate, 3 parts of butyl acetate, 4 parts of polymethyl methacrylate, solvent 10 parts, stirring and grinding, that is.
[0024] In step 1, the stirring speed is 200rpm, and the stirring time is 30min.
[0025] In step 2, the stirring speed is 100 rpm, and the stirring time is 40 min.
[0026] Stirrin...
Embodiment 2
[0029] A preparation method for marine anticorrosion paint, comprising the following steps:
[0030] Step 1, in parts by weight, take 4 parts of polyvinyl chloride, 2 parts of xylene formaldehyde resin, 5 parts of zinc citrate, and 3 parts of epoxy resin, add them to 14 parts of solvent, and stir to obtain mixture A;
[0031] Step 2, in parts by weight, add 2.5 parts of neoprene rubber, 2 parts of lecithin, 5 parts of sodium formaldehyde sulfoxylate, and 3 parts of chlorinated paraffin into the mixture A obtained in step 1, and stir to obtain mixture B;
[0032] Step 3, in parts by weight, add 4 parts of rutile titanium dioxide, 6 parts of dispersant, 3 parts of precipitated barium sulfate, 5 parts of butyl acetate, 5 parts of polymethyl methacrylate, solvent 15 parts, stirred and ground, that is to say.
[0033] In step 1, the stirring speed is 300 rpm, and the stirring time is 20 min.
[0034] In step 2, the stirring speed is 200rpm, and the stirring time is 30min.
[003...
Embodiment 3
[0038] A preparation method for marine anticorrosion paint, comprising the following steps:
[0039] Step 1, in parts by weight, take 6 parts of polyvinyl chloride, 2 parts of xylene formaldehyde resin, 4 parts of zinc citrate, and 3 parts of epoxy resin, add them to 17 parts of solvent, and stir to obtain mixture A;
[0040] Step 2, in parts by weight, add 3.5 parts of neoprene rubber, 2 parts of lecithin, 4 parts of sodium formaldehyde sulfoxylate, and 2 parts of chlorinated paraffin to the mixture A obtained in step 1, and stir to obtain mixture B;
[0041] Step 3, in parts by weight, add 4 parts of rutile titanium dioxide, 6 parts of dispersant, 5 parts of precipitated barium sulfate, 4 parts of butyl acetate, 5 parts of polymethyl methacrylate, solvent 15 parts, stirred and ground, that is to say.
[0042] In step 1, the stirring speed is 300 rpm, and the stirring time is 25 min.
[0043] In step 2, the stirring speed is 250rpm, and the stirring time is 25min.
[0044]...
PUM
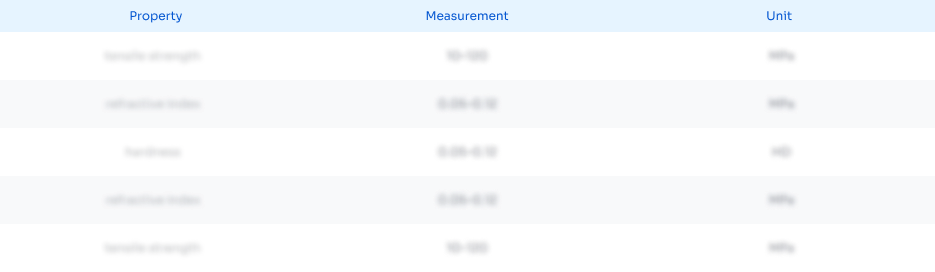
Abstract
Description
Claims
Application Information

- Generate Ideas
- Intellectual Property
- Life Sciences
- Materials
- Tech Scout
- Unparalleled Data Quality
- Higher Quality Content
- 60% Fewer Hallucinations
Browse by: Latest US Patents, China's latest patents, Technical Efficacy Thesaurus, Application Domain, Technology Topic, Popular Technical Reports.
© 2025 PatSnap. All rights reserved.Legal|Privacy policy|Modern Slavery Act Transparency Statement|Sitemap|About US| Contact US: help@patsnap.com