Valve bush carbonitriding thermal treatment process for high-pressure common rail
A high-pressure common rail and carbonitriding technology, used in heat treatment furnaces, heat treatment equipment, manufacturing tools, etc., to shorten labor time, reduce quenching deformation and cracking tendency, and improve hardenability.
- Summary
- Abstract
- Description
- Claims
- Application Information
AI Technical Summary
Problems solved by technology
Method used
Image
Examples
Embodiment 1
[0036] Embodiment one, preferably, the heat preservation time in step one is 160 minutes.
Embodiment 2
[0037] Embodiment 2, preferably, in step 2, the input rate of ammonia gas is 4 L / min, the input rate of propane is 10 L / min, and the input rate of methanol is 20 L / min.
Embodiment 3
[0038] Embodiment three, the tempering time in preferred step six is 165 minutes.
[0039] Further, the valve sleeve of the high-pressure common rail is made of GCr15 material.
[0040] Further, as image 3 , Figure 4 As shown, the station is a processing frame with an open top. In order to ensure the uniformity of carbonitriding, the bottom of the processing frame is flat, and the bottom and surroundings of the processing frame are hollow structures. The station Made of high-temperature-resistant stainless steel, the high-pressure common rail valve sleeves are laid flat and scattered in the processing frame.
[0041] Each process of the above heat treatment process is carried out on the automatic line of the multi-purpose furnace. The temperature control and programmed automatic operation are set by computer, and the process parameters can be monitored from the automatic recorder.
[0042]The high-pressure common rail valve sleeve products made of ball bearing steel (GC...
PUM
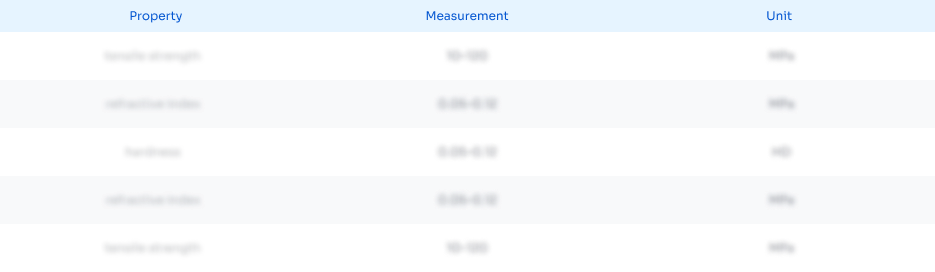
Abstract
Description
Claims
Application Information

- R&D
- Intellectual Property
- Life Sciences
- Materials
- Tech Scout
- Unparalleled Data Quality
- Higher Quality Content
- 60% Fewer Hallucinations
Browse by: Latest US Patents, China's latest patents, Technical Efficacy Thesaurus, Application Domain, Technology Topic, Popular Technical Reports.
© 2025 PatSnap. All rights reserved.Legal|Privacy policy|Modern Slavery Act Transparency Statement|Sitemap|About US| Contact US: help@patsnap.com