Modular foundation method
- Summary
- Abstract
- Description
- Claims
- Application Information
AI Technical Summary
Benefits of technology
Problems solved by technology
Method used
Image
Examples
Embodiment Construction
[0025] This improved method of forming a foundation uses a temporary prelevel coplanar support while installing a dynamic leveling permanent foundation. This improved method starts when a manufactured house arrives at the permanent site. The manufactured house has flooring assembly supported on its underside by horizontal parallel beams or joists that needs firmly grounded foundation support. The modular house may be a pair of elongated sections brought to the construction site by a truck. Preferably, the width of each module can fit on a single flatbed truck. The sections of the modular house are placed upon temporary supports by a crane and leveled. The buttress assemblies 210 arrive at the job site fully assembled and welded including the tubular stanchion 212, L-shaped bracket 211, vertical flange 214, base plate 217, anchor bolt head 218 or J shaped uplift bars, and steel tabs 219. Each of the sections of the modular house is joined to the others. Underneath the house the mate ...
PUM
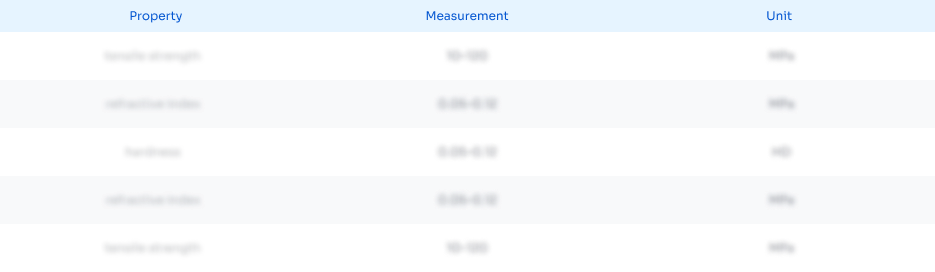
Abstract
Description
Claims
Application Information

- R&D
- Intellectual Property
- Life Sciences
- Materials
- Tech Scout
- Unparalleled Data Quality
- Higher Quality Content
- 60% Fewer Hallucinations
Browse by: Latest US Patents, China's latest patents, Technical Efficacy Thesaurus, Application Domain, Technology Topic, Popular Technical Reports.
© 2025 PatSnap. All rights reserved.Legal|Privacy policy|Modern Slavery Act Transparency Statement|Sitemap|About US| Contact US: help@patsnap.com