One-step catalytic synthesis method for 2-methoxyethanol benzoate
A technology of ethylene glycol methyl ether and benzoate, applied in the field of fine chemicals, can solve the problems of easy environmental pollution, difficult product processing, complicated processes, etc., and achieves less environmental pollution, high reactivity, and good product selectivity. Effect
- Summary
- Abstract
- Description
- Claims
- Application Information
AI Technical Summary
Problems solved by technology
Method used
Image
Examples
Embodiment 1
[0026] 163.8g methyl benzoate and 3.2g catalyst (magnesium-aluminum-manganese salt cation molar ratio is Mg:Al:Mn=1:1:0.04) are added in the reactor that volume is 2L, airtight stirring, with N 2 Replace the air in the kettle, heat up, and when the temperature reaches 120°C, continue to feed 52.86g of ethylene oxide into the reaction kettle, the pressure in the reaction kettle is 0.15-0.50MPa, and the reaction temperature is constant at 120°C. The reaction raw material mol ratio is methyl benzoate: oxirane=1:1. Ethylene oxide conversion rate is 76.47%, ethylene glycol methyl ether benzoic acid ester productive rate is 26.40%, diethylene glycol methyl ether benzoic acid ester productive rate is 26.07%, triethylene glycol methyl ether benzoic acid The ester yield was 14.47%.
Embodiment 2
[0028] 164.0g methyl benzoate and 2.9g catalyst (magnesium aluminum manganese salt cation molar ratio is Mg:Al:Mn=1:1:0.04) are added in the reaction kettle that volume is 2L, airtight stirring, with N 2 Replace the air in the kettle, heat up, and when the temperature reaches 120°C, continue to feed 26.43g of ethylene oxide into the reactor, the pressure in the reactor is 0.20-0.45MPa, and the reaction temperature is constant at 120°C. The molar ratio of the reaction raw materials is methyl benzoate: oxirane=2:1. Ethylene oxide conversion rate is 85.23%, ethylene glycol methyl ether benzoic acid ester productive rate is 33.83%, diethylene glycol methyl ether benzoic acid ester productive rate is 29.93%, triethylene glycol methyl ether benzoic acid ester The ester yield was 16.19%.
Embodiment 3
[0030] 245.2g of methyl benzoate and 4.1g of catalyst (magnesium-aluminum-manganese salt cation molar ratio is Mg:Al:Mn=1:1:0.04) were added into a reaction kettle with a volume of 2L, sealed and stirred, and heated with N 2 Replace the air in the kettle, heat up, and when the temperature reaches 120°C, continue to feed 26.38g of ethylene oxide into the reactor, the pressure in the reactor is 0.15-0.45MPa, and the reaction temperature is constant at 120°C. The molar ratio of the reaction raw materials is methyl benzoate: oxirane=3:1. Ethylene oxide conversion rate is 86.39%, ethylene glycol methyl ether benzoic acid ester productive rate is 46.99%, diethylene glycol methyl ether benzoic acid ester productive rate is 25.95%, triethylene glycol methyl ether benzoic acid ester The ester yield was 9.84%.
PUM
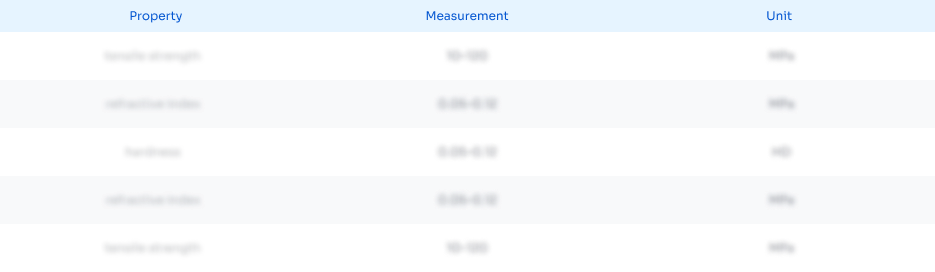
Abstract
Description
Claims
Application Information

- R&D
- Intellectual Property
- Life Sciences
- Materials
- Tech Scout
- Unparalleled Data Quality
- Higher Quality Content
- 60% Fewer Hallucinations
Browse by: Latest US Patents, China's latest patents, Technical Efficacy Thesaurus, Application Domain, Technology Topic, Popular Technical Reports.
© 2025 PatSnap. All rights reserved.Legal|Privacy policy|Modern Slavery Act Transparency Statement|Sitemap|About US| Contact US: help@patsnap.com