Method for synthesizing diethylene glycol ethyl ether acrylate
A technology of diethylene glycol ethyl ether and methacrylate, which is applied in the field of fine chemicals, can solve the problems of backward production technology and low output, and achieve the effects of low environmental pollution, high catalytic activity and mild reaction conditions
- Summary
- Abstract
- Description
- Claims
- Application Information
AI Technical Summary
Problems solved by technology
Method used
Image
Examples
Embodiment 1
[0021] 111.9g methacrylic acid, 134.17g diethylene glycol ether, 12.3g catalyst S 2 o 8 2- / ZrO 2 -SiO 2 , 36.9g toluene, and 1.23g phenothiazine were added to a four-necked flask, the vacuum degree was -0.04~-0.045MPa, the temperature was raised to reaction reflux, and the temperature was continuously raised to 140°C, and the water in the water separator was separated in time, and the reaction raw materials The molar ratio is methacrylic acid: diethylene glycol ether = 1.3:1; the amount of catalyst is 5% of the total mass of raw materials; the amount of water-carrying agent is 15% of the total mass of raw materials; the amount of polymerization inhibitor is 5% of the total mass of raw materials , wherein the reaction temperature is 140°C. The conversion rate of diethylene glycol ethyl ether was 69.04%, and the yield of diethylene glycol ethyl ether methacrylate was 68.15%.
Embodiment 2
[0023] 111.9g methacrylic acid, 134.17g diethylene glycol ether, 12.3g catalyst S 2 o 8 2- / ZrO 2 -SiO 2 , 36.9g toluene, and 1.23g phenothiazine were added to a four-neck flask, the vacuum degree was -0.04~-0.045MPa, the temperature was raised to reaction reflux, and the temperature was continuously raised to 145°C, and the water in the water separator was separated in time, and the reaction raw materials The molar ratio is methacrylic acid: diethylene glycol ether = 1.3:1; the amount of catalyst is 5% of the total mass of raw materials; the amount of water-carrying agent is 15% of the total mass of raw materials; the amount of polymerization inhibitor is 5% of the total mass of raw materials , wherein the reaction temperature is 145°C. The conversion rate of diethylene glycol ethyl ether was 81.88%, and the yield of diethylene glycol ethyl ether methacrylate was 80.19%.
Embodiment 3
[0025] 111.9g methacrylic acid, 134.17g diethylene glycol ether, 12.3g catalyst S 2 o 8 2- / ZrO 2 -SiO 2 , 36.9g toluene, and 1.23g phenothiazine were added to a four-neck flask, the vacuum degree was -0.04~-0.045MPa, the temperature was raised to reaction reflux, and the temperature was continuously raised to 150°C, and the water in the water separator was separated in time, and the reaction raw materials The molar ratio is methacrylic acid: diethylene glycol ether = 1.3:1; the amount of catalyst is 5% of the total mass of raw materials; the amount of water-carrying agent is 15% of the total mass of raw materials; the amount of polymerization inhibitor is 5% of the total mass of raw materials , wherein the reaction temperature is 150°C. The conversion rate of diethylene glycol ether was 90.57%, and the yield of diethylene glycol ether methacrylate was 86.62%.
PUM
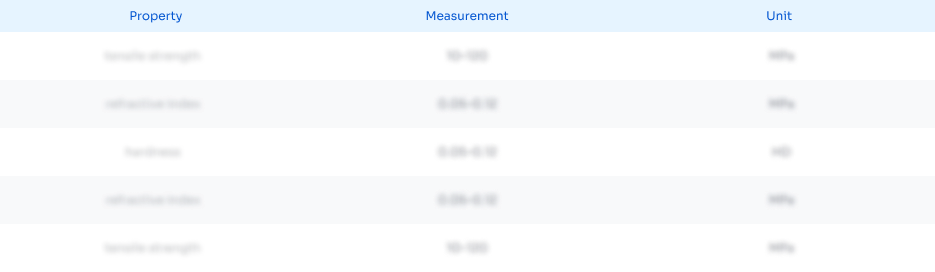
Abstract
Description
Claims
Application Information

- R&D Engineer
- R&D Manager
- IP Professional
- Industry Leading Data Capabilities
- Powerful AI technology
- Patent DNA Extraction
Browse by: Latest US Patents, China's latest patents, Technical Efficacy Thesaurus, Application Domain, Technology Topic, Popular Technical Reports.
© 2024 PatSnap. All rights reserved.Legal|Privacy policy|Modern Slavery Act Transparency Statement|Sitemap|About US| Contact US: help@patsnap.com