Oil fume resistant polycarbonate material, preparation method and application thereof
A technology of polycarbonate and oil fume, applied in the field of polycarbonate materials, can solve the problem of oil resistance not being improved, and achieve the effects of improved oil fume cracking resistance, oil cracking resistance, and good impact toughness
- Summary
- Abstract
- Description
- Claims
- Application Information
AI Technical Summary
Problems solved by technology
Method used
Image
Examples
Embodiment 1~3
[0042] Embodiments 1 to 3 relate to a kind of oil fume-resistant polycarbonate material, and the contents of each formula component of the material are as shown in Table 1; wherein, the PC resin is selected from the resin of LG-DOWPC201-10; the carboxylated nitrile rubber is selected from Krynac211 (Canada SARNIA company), its acrylonitrile mass percentage content is between 31%~35%; Flame retardant selects the BC58 (brominated polycarbonate flame retardant) of U.S. Great Lakes Company for use; Antioxidant selects Iraanox1076 and Iraanox168 of Ciba Company for use The compound, its mass ratio is 1:1; Lubricant adopts PETS to be commercially available pentaerythritol ester.
[0043] Its preparation steps are as follows:
[0044] 1) carboxyl nitrile rubber Krynac211 and ethylene methyl acrylate copolymer ( 1330) after mixing with the ratio of mass ratio 4:1, join in the kneader and fully knead, then carry out pelletizing, obtain the nitrile rubber masterbatch;
[0045] 2) Add t...
Embodiment 4
[0065] Carboxylated nitrile rubber 1072 (Taiwan Nandi, acrylonitrile mass percentage content 27%) and ethylene methyl acrylate copolymer ( 1330) after mixing with the ratio of mass ratio 4:1, add in the kneader and fully knead, then carry out pelletizing, obtain the nitrile rubber masterbatch.
[0066] 10 parts of prepared nitrile rubber master batches were mixed with 81.1 parts of polycarbonate resin (PC201-10), 8 parts of flame retardant (BC58), 0.5 parts of compound antioxidant (1076 / 168=1:1) and Dow Corning Add 0.4 parts of silicone powder (4-7081) into a high-speed mixing mixer, first stir at a low speed of 1000rpm for 2 minutes, then stir at a high speed of 1500rpm for 3 minutes and mix well. The resulting mixture is fed through the main feeding port of the twin-screw extruder, extruded and pelletized.
[0067] The temperature settings of the twin-screw extruder used are: zone 1: 250°C, zone 2: 265°C, zone 3: 265°C, zone 4: 250°C, zone 5: 240°C, zone 6: 240°C, zone 7: ...
Embodiment 5
[0069] Carboxylated nitrile rubber 3245C (Taiwan Nandi, acrylonitrile mass percentage content 32%) and ethylene methyl acrylate copolymer ( 1330) mixed at a mass ratio of 4:1, then added to a kneader and fully kneaded, and then pelletized.
[0070] 10 parts of prepared nitrile rubber masterbatch and 80.5 parts of polycarbonate resin (PC201-10), 8 parts of flame retardant (BC58), 0.5 part of compound antioxidant (1076 / 168=1:1) and Dow Corning Add 1 part of silicone powder (4-7081) into a high-speed mixing mixer, first stir at a low speed of 1000rpm for 2 minutes, and then stir at a high speed of 1500rpm for 3 minutes to mix well. The resulting mixture is fed through the main feeding port of the twin-screw extruder, extruded and pelletized.
[0071] The temperature settings of the twin-screw extruder used are: zone 1: 250°C, zone 2: 265°C, zone 3: 265°C, zone 4: 250°C, zone 5: 240°C, zone 6: 240°C, zone 7: 240 ℃, 8th zone: 240℃, 9th zone: 240℃, die head: 250℃, screw speed 450...
PUM
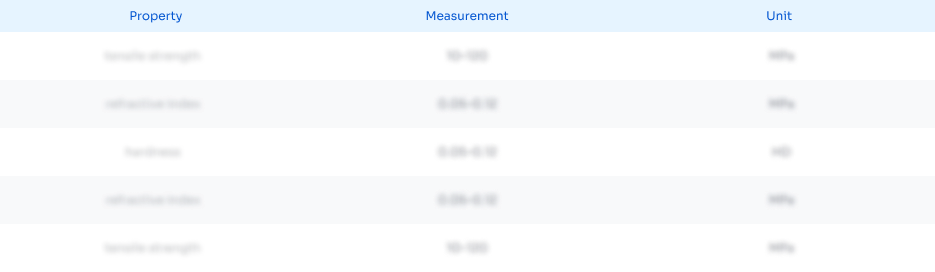
Abstract
Description
Claims
Application Information

- Generate Ideas
- Intellectual Property
- Life Sciences
- Materials
- Tech Scout
- Unparalleled Data Quality
- Higher Quality Content
- 60% Fewer Hallucinations
Browse by: Latest US Patents, China's latest patents, Technical Efficacy Thesaurus, Application Domain, Technology Topic, Popular Technical Reports.
© 2025 PatSnap. All rights reserved.Legal|Privacy policy|Modern Slavery Act Transparency Statement|Sitemap|About US| Contact US: help@patsnap.com