Deformation control method in rigid heat-insulating tile coating forming process
A molding process and deformation control technology, which is applied in the field of preparation of aircraft thermal protection materials, can solve the problems of deformation of the base material, the specific size and deformation of the sample are not given, and the deformation of the rigid heat insulation tile is not specifically mentioned. To achieve the effect of reducing thermal stress, reducing deformation, avoiding damage and destruction
- Summary
- Abstract
- Description
- Claims
- Application Information
AI Technical Summary
Problems solved by technology
Method used
Image
Examples
Embodiment 1
[0048] The thickness of the sample is required to be 10mm, and the high-temperature sintering heat treatment adopts the overall sintering heat treatment method.
[0049] The ceramic matrix material of the rigid insulation tile is prepared by a mixed fiber of 80% oxidized fiber and 20% mullite fiber, and the density is 0.33g / cm 3 , initially processed into a sample of 200 × 200 × 20mm, the mass ratio of each component in the coating slurry is: borosilicate glass powder: boron oxide: tantalum disilicide: clay: water = 60:30:8:2: 500, mixed with a ball mill for 3 hours, coated on the upper surface of the base material (the upper and lower surface areas are the largest) and the side, and the side is coated with 6mm, and the surface density of the coating obtained after spraying and drying is 0.025g / cm 2 , in a high-temperature furnace at 1150 ° C for 15 minutes of overall sintering heat treatment, after cooling to room temperature, using a milling machine to process the formed coa...
Embodiment 2
[0051] The thickness of the sample is required to be 15mm, and the high-temperature sintering heat treatment adopts the overall sintering heat treatment method.
[0052] The ceramic matrix material of the rigid insulation tile is prepared by a mixed fiber of 80% oxidized fiber and 20% mullite fiber, and the density is 0.33g / cm 3 , processed into a sample piece of 200×200×20mm, the mass ratio of each component in the coating slurry is: borosilicate glass powder: boron oxide: tantalum disilicide: clay: water=60:30:8:2: 500, mixed with a ball mill for 3 hours, coated on the upper surface of the base material (the upper and lower surface area is the largest) and the side, and the side is coated with 10mm, and the surface density of the coating obtained after spraying and drying is 0.025g / cm 2, in a high-temperature furnace at 1150 ° C for 15 minutes of overall sintering heat treatment, after cooling to room temperature, using a milling machine for final processing to a thickness o...
Embodiment 3
[0054] The thickness of the sample is required to be 10mm, and the high-temperature sintering heat treatment adopts a single-side heat treatment method.
[0055] The ceramic matrix material of the rigid insulation tile is prepared by a mixed fiber of 80% oxidized fiber and 20% mullite fiber, and the density is 0.33g / cm 3 , processed into a sample piece of 200×200×20mm, the mass ratio of each component in the coating slurry is: borosilicate glass powder: boron oxide: tantalum disilicide: clay: water=60:30:8:2: 500, mixed with a ball mill for 3 hours, coated on the upper surface of the base material (the upper and lower surface areas are the largest) and the side, and the side is coated with 6mm, and the surface density of the coating obtained after spraying and drying is 0.025g / cm 2 , the upper surface was sintered and heat-treated at 1150°C for 15 minutes at the entrance of the high-temperature furnace, and after cooling to room temperature, it was finally machined to a thickn...
PUM
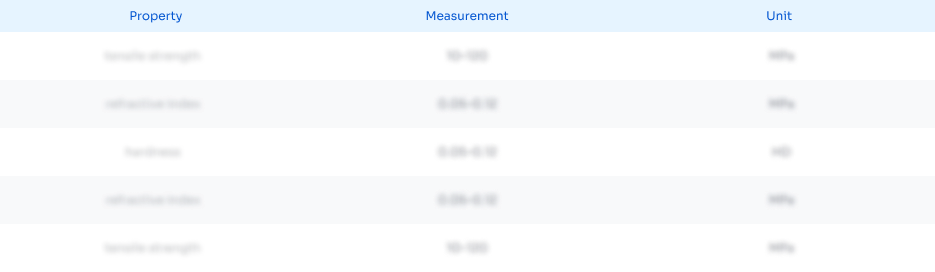
Abstract
Description
Claims
Application Information

- R&D
- Intellectual Property
- Life Sciences
- Materials
- Tech Scout
- Unparalleled Data Quality
- Higher Quality Content
- 60% Fewer Hallucinations
Browse by: Latest US Patents, China's latest patents, Technical Efficacy Thesaurus, Application Domain, Technology Topic, Popular Technical Reports.
© 2025 PatSnap. All rights reserved.Legal|Privacy policy|Modern Slavery Act Transparency Statement|Sitemap|About US| Contact US: help@patsnap.com