Dyeing and finishing process for linen and cotton blended fiber fabric
A technology of blended fabrics and blended fibers, which is applied in the field of dyeing and finishing technology, can solve the problems of affecting the brightness and aesthetics of dyed fabrics, poor dyeing effect of natural dyes, and damage to the ecological environment, and achieves good desizing effect, variable treatment temperature, The effect of reducing environmental pollution
- Summary
- Abstract
- Description
- Claims
- Application Information
AI Technical Summary
Problems solved by technology
Method used
Examples
Embodiment 1
[0045] A dyeing and finishing process of flax-cotton blended fiber fabric includes the following steps:
[0046] (1) Pre-treatment: Pre-treatment of flax-cotton blended fabric, specifically: 1g / L urea, TF-104M 4.5g / L non-phosphorus degreasing agent, 8g / L scouring enzyme, 8g / L 30% hydrogen peroxide, Snail enzyme 8g / L, α-amylase 8g / L, degumming aid 4.5g / L, ultrasonic treatment in 40℃ ultrasonic water bath for 1-2min, bath ratio 30:1, ultrasonic frequency 45Hz, the treatment is over Then refill it with clean water, wash it twice, and then dry;
[0047] (2) Pre-formation: pre-form treatment of linen-cotton blended fabric, add heat yellowing agent FK-1618g / L when setting, setting temperature is 150℃, speed is 20m / min, overfeeding is 5%;
[0048] (3) Modification treatment: Put the finalized linen-cotton blended fabric into a water bath for treatment. The water bath contains 3g / L of chitosan and 4g / L of 2,3-epoxypropyltrimethylammonium chloride. 3-chloro-2-hydroxypropyltrimethylammonium ...
Embodiment 2
[0064] A dyeing and finishing process of flax-cotton blended fiber fabric includes the following steps:
[0065] (1) Pre-treatment: pre-treatment of flax-cotton blended fabric, specifically: urea 1.2g / L, non-phosphorus degreasing agent TF-104M 5g / L, scouring enzyme 9g / L, 30% hydrogen peroxide 9g / L, snail Enzyme 9g / L, α-amylase 9g / L, degumming aid 5g / L, ultrasonic treatment in 40℃ ultrasonic water bath for 1-2min, bath ratio of 30:1, ultrasonic frequency of 45Hz, restart after treatment Pour clean water and wash twice, then dry;
[0066] (2) Pre-formation: pre-form treatment of flax-cotton blended fabric, add heat yellowing agent FK-1619g / L when setting, setting temperature is 155℃, speed is 25m / min, overfeeding 8%;
[0067] (3) Modification treatment: Put the finalized flax-cotton blended fabric into a water bath for treatment. The water bath contains 4g / L of chitosan and 5g / L of 2,3-epoxypropyltrimethylammonium chloride. 3-chloro-2-hydroxypropyltrimethylammonium chloride 5g / L, hyd...
Embodiment 3
[0083] A dyeing and finishing process of flax-cotton blended fiber fabric includes the following steps:
[0084] (1) Pre-treatment: pre-treatment of flax-cotton blended fabric, specifically: urea 1.5g / L, non-phosphorus degreasing agent TF-104M 5.5g / L, scouring enzyme 10g / L, 30% hydrogen peroxide 10g / L , Snail enzyme 10g / L, α-amylase 10g / L, degumming aid 5.5g / L, ultrasonic treatment in 40℃ ultrasonic water bath for 1-2min, bath ratio 30:1, ultrasonic frequency 45Hz, treatment After finishing, pour clean water and wash twice, then dry;
[0085] (2) Pre-formation: pre-form treatment of flax-cotton blended fabric, add heat yellowing agent FK-16110g / L when setting, setting temperature is 160℃, vehicle speed is 30m / min, overfeeding 10%;
[0086] (3) Modification treatment: Put the finalized flax-cotton blended fabric into a water bath for treatment. The water bath contains chitosan 5g / L and 2,3-epoxypropyltrimethylammonium chloride 6g / L. 3-chloro-2-hydroxypropyltrimethylammonium chloride...
PUM
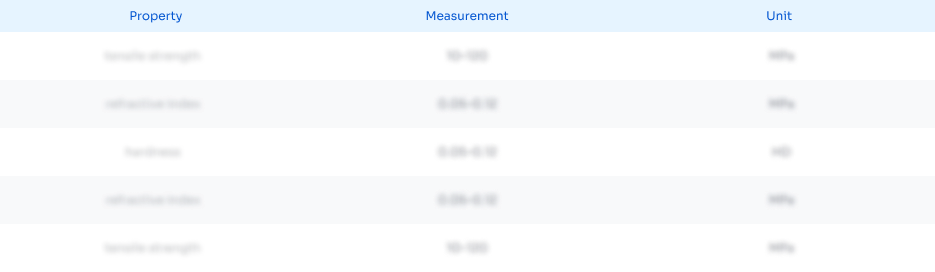
Abstract
Description
Claims
Application Information

- R&D Engineer
- R&D Manager
- IP Professional
- Industry Leading Data Capabilities
- Powerful AI technology
- Patent DNA Extraction
Browse by: Latest US Patents, China's latest patents, Technical Efficacy Thesaurus, Application Domain, Technology Topic, Popular Technical Reports.
© 2024 PatSnap. All rights reserved.Legal|Privacy policy|Modern Slavery Act Transparency Statement|Sitemap|About US| Contact US: help@patsnap.com