Vanadium iron slag-thermal power plant coal ash evaporative pattern casting coating and preparation method thereof
A technology of lost foam casting and thermal power plants, which is applied to casting molding equipment, coatings, casting molds, etc. It can solve the problems of restricting the development of lost foam casting technology, the poor commercialization of coatings, and the increase in production costs, so as to achieve structural stability, Effects of improving fire resistance limit, cohesiveness and dispersibility
- Summary
- Abstract
- Description
- Claims
- Application Information
AI Technical Summary
Problems solved by technology
Method used
Examples
Embodiment 1
[0042] A vanadium-iron slag-thermal power plant fly ash lost foam casting coating is characterized in that, the lost foam casting coating is made up of the following raw materials in parts by weight:
[0043] 55 parts of ferrovanadium slag
[0044] Thermal power plant fly ash 53 parts
[0045] 25 parts of magnesia
[0046] 7 parts diatomaceous earth
[0047] Silicon carbide 6 parts
[0048] 2 parts high alumina fine powder
[0049] brucite 2 parts
[0050] Tantalum carbide 2 parts
[0051] Aluminum nitride 2 parts
[0052] Boron nitride 2 parts
[0053] 4 parts of γ-(methacryloyloxy)propyltrimethoxysilane
[0054] 6 parts of bis(dilauryl phosphite)tetraoxoctoxy titanate
[0055] 2 parts of isobutanol etherified melamine methyl ether resin
[0056] Dicumyl peroxide 0.3 parts
[0057] 0.4 parts of polyvinyl alkyl alcohol ether
[0058] Tertiary vinegar emulsion 0.3 part
[0059] carbon fiber 2 parts
[0060] 1 part dextrin
[0061] Sodium alginate 2 parts
[0062...
Embodiment 2
[0071] A vanadium-iron slag-thermal power plant fly ash lost foam casting coating is characterized in that, the lost foam casting coating is made up of the following raw materials in parts by weight:
[0072] 64 parts of ferrovanadium slag
[0073] Thermal power plant fly ash 57 parts
[0074] 33 parts of magnesia
[0075] 10 parts diatomaceous earth
[0076] Silicon carbide 8 parts
[0077] 6 parts of high alumina fine powder
[0078] brucite 5 parts
[0079] Tantalum carbide 6 parts
[0080] Aluminum nitride 4 parts
[0081] Boron nitride 4 parts
[0082] 7 parts of γ-(methacryloyloxy)propyltrimethoxysilane
[0083] 10 parts of bis(dilauryl phosphite)tetraoxoctoxy titanate
[0084] 4 parts of isobutanol etherified melamine methyl ether resin
[0085] 0.6 parts of dicumyl peroxide
[0086] 0.6 parts of polyvinyl alkyl alcohol ether
[0087] Tertiary vinegar emulsion 0.6 parts
[0088] Carbon fiber 3 parts
[0089] 3 parts dextrin
[0090] 3 parts sodium alginat...
PUM
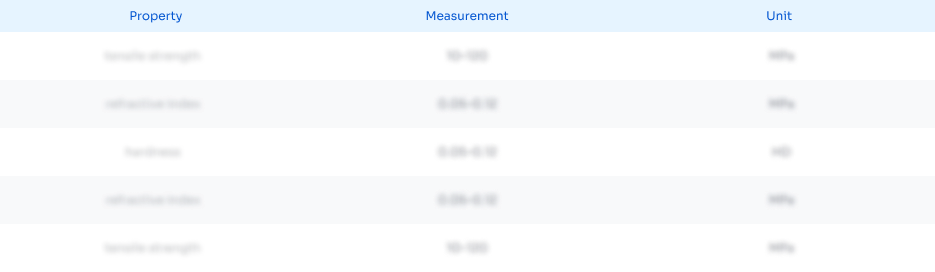
Abstract
Description
Claims
Application Information

- R&D
- Intellectual Property
- Life Sciences
- Materials
- Tech Scout
- Unparalleled Data Quality
- Higher Quality Content
- 60% Fewer Hallucinations
Browse by: Latest US Patents, China's latest patents, Technical Efficacy Thesaurus, Application Domain, Technology Topic, Popular Technical Reports.
© 2025 PatSnap. All rights reserved.Legal|Privacy policy|Modern Slavery Act Transparency Statement|Sitemap|About US| Contact US: help@patsnap.com