Method for manufacturing large-sized 5083 aluminum alloy slab ingot
A manufacturing method and large-scale technology, applied in the field of aluminum alloy manufacturing, can solve the problems of low yield and low production efficiency, and achieve the effects of improving yield and reducing production costs.
- Summary
- Abstract
- Description
- Claims
- Application Information
AI Technical Summary
Problems solved by technology
Method used
Image
Examples
Embodiment 1
[0023] In this embodiment, the 5083 aluminum alloy wide and large size (2520mm*620mm) slab for hot rolling contains the following chemical elements in mass percentage: Si0.15%, Fe0.35%, Cu0.10%, Mn0.45%~0.80% , Mg4.10%~4.70%, Cr0.05~0.2%, Na≤0.0005%, Zn0.10%, Ti0.10%, single impurity≤0.05%, total impurity≤0.15%, and the rest is Al.
[0024] The manufacturing method step of above-mentioned slab is as follows:
[0025] A. Prepare raw and auxiliary materials: Weigh aluminum ingots, sodium-free alloy additives and waste materials respectively. The sodium-free alloy additives include iron agent, manganese agent, fast-melting silicon, chromium agent, and magnesium ingots, and the ratio of waste materials is 30%;
[0026] B. Melting and standing: the melting furnace gas temperature is 1050°C-1065°C during smelting, the melt temperature is kept between 700°C-715°C, the converter temperature is controlled at 735°C, and the refining temperature after transferring to the holding furnace ...
Embodiment 2
[0035] The chemical element composition and ratio of the slab for hot rolling of the 5083 aluminum alloy with wide width and large specification (2520mm*620mm) in this embodiment are the same as those in Embodiment 1.
[0036] The manufacturing method steps of the slab of the present embodiment are as follows:
[0037] A. Prepare raw and auxiliary materials: Weigh aluminum ingots, sodium-free alloy additives and waste materials respectively. The sodium-free alloy additives include iron agent, manganese agent, fast-melting silicon, chromium agent, and magnesium ingots, and the ratio of waste materials is 50%;
[0038] B. Melting and standing: the melting furnace gas temperature is 1065°C-1080°C during smelting, the melt temperature is kept between 715°C-730°C, the converter temperature is controlled at 740°C, and the refining temperature after transferring to the holding furnace is 725°C °C, the refining time is 50min, and the refining gas is a nitrogen-chlorine mixed gas, wher...
Embodiment 3
[0046] The chemical element composition and ratio of the slab for hot rolling of the 5083 aluminum alloy with wide width and large specification (2520mm*620mm) in this embodiment are the same as those in Embodiment 1.
[0047] The manufacturing method steps of the slab of the present embodiment are as follows:
[0048] A. Prepare raw and auxiliary materials: Weigh aluminum ingots, sodium-free alloy additives and waste materials respectively. The sodium-free alloy additives include iron agent, manganese agent, fast-melting silicon, chromium agent, and magnesium ingots, and the ratio of waste materials is 70%;
[0049] B. Melting and standing: the melting furnace gas temperature is 1080°C-1100°C during smelting, the melt temperature is kept between 730°C-750°C, the converter temperature is controlled at 745°C, and the refining temperature after transferring to the holding furnace is 730°C ℃, the refining time is 60min, and the refining gas is nitrogen-chlorine mixed gas, wherein...
PUM
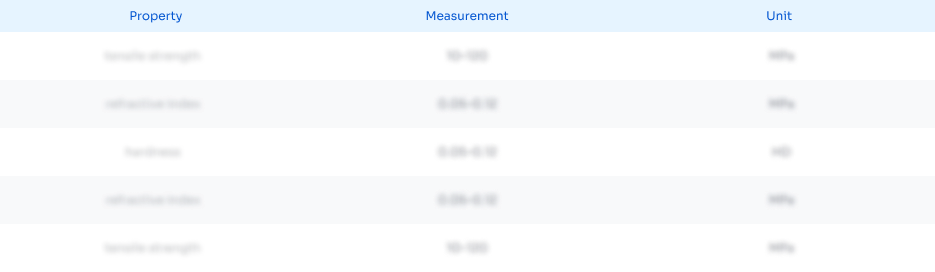
Abstract
Description
Claims
Application Information

- Generate Ideas
- Intellectual Property
- Life Sciences
- Materials
- Tech Scout
- Unparalleled Data Quality
- Higher Quality Content
- 60% Fewer Hallucinations
Browse by: Latest US Patents, China's latest patents, Technical Efficacy Thesaurus, Application Domain, Technology Topic, Popular Technical Reports.
© 2025 PatSnap. All rights reserved.Legal|Privacy policy|Modern Slavery Act Transparency Statement|Sitemap|About US| Contact US: help@patsnap.com