Large-section hollow profile extrusion forming method and device with small-opening die utilized
An extrusion molding and large cross-section technology, which is applied in the field of large cross-section hollow profile extrusion molding, can solve the problems of high difficulty in equipment processing, increased difficulty in mandrel and die processing, complex and heavy equipment, etc., to improve the quality of internal and external surfaces , easy to realize the effect of control and simple equipment principle
- Summary
- Abstract
- Description
- Claims
- Application Information
AI Technical Summary
Problems solved by technology
Method used
Image
Examples
Embodiment 1
[0032] This embodiment is a method for extrusion molding of a large cross-section hollow profile using a small die. The blank extruded from the die is blown by compressed air to form a layer of narrow slit-shaped air cushion inside the blank, which has the same hollow shape as the product. The further expansion of the air cushion makes the blank stick to the inner wall of the vacuum sizing sleeve, and under the synergistic effect of the air cushion and vacuum setting, the hollow pipe product is formed, and the continuous production of large cross-section hollow profiles is realized by using a small die.
[0033] This method can be used to form round tubes (such as Figure 2a shown), square tube (such as Figure 2b shown), triangular tube (such as Figure 2c shown), oval special-shaped tube (such as Figure 2d shown) or other shaped tubes.
Embodiment 2
[0035] This embodiment is a large-section hollow profile extrusion molding equipment using a small die, as shown in FIG. 2 , including an extruder 1, a die head 12 and a vacuum cooling and shaping device 13 connected in sequence.
[0036]A blowing device is provided inside the die head, and the blowing device includes a mandrel 9, an air inlet pipe 2 and an inner cooling air plug 3. The head of the cold air plug is arranged in the space between the die head and the vacuum cooling and shaping device, and the flow channel for forming the blank is between the outer wall of the mandrel and the die head. Wherein, the inner cooling air plug is a hollow structure, including a connected rod part 3-1 and a head part 3-2, the rod part is in the shape of a straight tube, the head part is in the shape of a cone, and the side wall of the head part is provided with a through hole 3-3. The rod part runs through the whole air inlet pipe, the end of the rod part close to the vacuum cooling and...
PUM
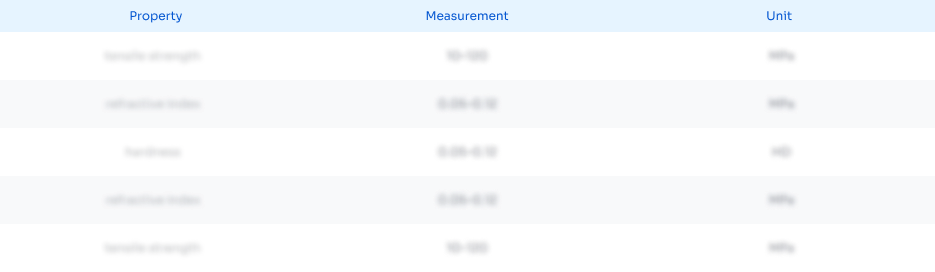
Abstract
Description
Claims
Application Information

- R&D
- Intellectual Property
- Life Sciences
- Materials
- Tech Scout
- Unparalleled Data Quality
- Higher Quality Content
- 60% Fewer Hallucinations
Browse by: Latest US Patents, China's latest patents, Technical Efficacy Thesaurus, Application Domain, Technology Topic, Popular Technical Reports.
© 2025 PatSnap. All rights reserved.Legal|Privacy policy|Modern Slavery Act Transparency Statement|Sitemap|About US| Contact US: help@patsnap.com