Special grinding machine for in-situ grinding of pinch roller of shearing machine
A special grinding machine and pinch roller technology, which is applied in the direction of grinding machines, machine tools designed for grinding the rotating surface of workpieces, grinding/polishing equipment, etc., can solve the wear deformation, adhesion, and thermal fatigue of the outer surface of the pinch roller and other problems, to achieve the effect of grinding and dressing, high positioning accuracy and high processing accuracy
- Summary
- Abstract
- Description
- Claims
- Application Information
AI Technical Summary
Problems solved by technology
Method used
Image
Examples
Embodiment Construction
[0026] The present invention will be described in detail below in conjunction with the accompanying drawings and specific embodiments.
[0027] The special grinding machine for in-position grinding of the outer circle of the pinch roller of the shearing machine of the present invention has a structure such as figure 1 As shown, it includes a right-angled trapezoidal block-shaped bed 4, a cross slide 12 is arranged close to the inclined surface of the bed 4, an adjustment block 14 is provided on the workbench of the cross slide 12, and a grinding mechanism is installed on the adjustment block 14 , the upper bottom surface of the bed 4 is provided with a pinch roller fixing frame, and the pinch roller fixing frame is provided with a threaded groove 7 for fixing the pinch roller, the cross slide 12 is parallel to the inclined plane of the bed 4, and the pinch roller fixing frame It is located at the center of the bed 4 upper bottom.
[0028] Such as figure 2 As shown, the grin...
PUM
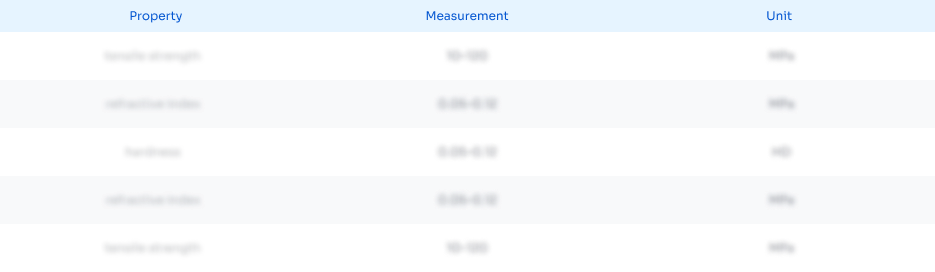
Abstract
Description
Claims
Application Information

- R&D
- Intellectual Property
- Life Sciences
- Materials
- Tech Scout
- Unparalleled Data Quality
- Higher Quality Content
- 60% Fewer Hallucinations
Browse by: Latest US Patents, China's latest patents, Technical Efficacy Thesaurus, Application Domain, Technology Topic, Popular Technical Reports.
© 2025 PatSnap. All rights reserved.Legal|Privacy policy|Modern Slavery Act Transparency Statement|Sitemap|About US| Contact US: help@patsnap.com